未来的汽车什么样—车身的轻量化
By www.carbonfiber.com.cn
汽车的轻量化,不仅包括减轻车身的重量,还涉及对车身结构的整合,重新设计,达到最佳的轻量效果。在保证汽车的强度和安全性能的前提下,尽可能地降低汽车的整备质量,从而提高汽车的动力性,减少燃料消耗,降低排气污染。实验证明,若汽车整车重量降低10%,燃油效率可提高6%—8%;汽车整备质量每减少100公斤,百公里油耗可降低0.3—0.6升;汽车重量降低1%,油耗可降低0.7%。
轻量化的车身设计,要求车身结构更加合理,车内空间也会更大。缩小尺寸的汽车还可以节省物料的使用,应用新型材料使车身变轻以后使车辆行驶更加快速,节能。
NO.1 碳纤维作为汽车新兴材料的出现,大大减轻了汽车的重量
碳纤维用在一体式车架
这种一体式车架,早期用在飞机火箭上,后来被f1赛车成功推广,被称作单体壳,至此在跑车界蔓延开来。碳纤维的承载式车身能承受更大的拉应力,在目前的极速范围内,这个封闭的座舱,能够在车身在高速冲撞,车体彻底支解后,保证驾驶者的绝对安全。
碳纤维复合材质车架
从图中我们可以看出,左边的金属车架和右边的碳纤维车架差别明显,碳纤维车架不同于传统的焊接或者铆接技术,结合新材料的特点和制造工艺,我们所看到的碳纤维车身都像盒子一样,和普通的承载式车身的区别还是很大。
代表车型:兰博基尼AventadorLP700-4
这款兰博基尼旗舰款超级跑车颇具未来风格,车舱完全以碳纤维制造而成,并配以硬壳式结构。其承载结构则为“单壳体”设计,在构造上可作为单一部件发挥作用,从而充分利用碳纤维强化材料的超强刚度。
当然,“单壳体”的称谓只是一种形容,新型兰博基尼硬壳式车体其实是由一系列功能各异的独立部件构造而成,运用“编织”(Braiding)技术制成的加强件就是其一。“编织”是业内最有效的碰撞能量吸收技术之一。尽管是由众多部件集合而成,但经过固化之后,这种结构就能化为单一部件统一工作,底部结构称为“骨架”,与整个车顶都囊括在其中。并且,该车全硬壳式结构重量仅有145.5公斤(324.5磅)。
兰博基尼AventadorLP700-4 碳纤维一体车架
虽然一体式碳纤维车架很坚韧,但有受力向度的问题,即整体中的某些部位不太能受力。每辆车都根据自己整体的情况特别设计车架,如F50的车架将后悬架直接连接在发动机及变速器上,再将整个发动机悬架结构嵌入车体内,其车架只重102kg,而抗扭度高达3550kgm/degree。这种设计可以营造极轻量的悬架重量,但同时会有较大的发动机振荡传入车厢。
但是碳纤维不适合做越野车车架,因为越野车车架通常都需要允许非常大的变形和扭动等。目前的碳纤维太过于脆,没有良好的韧性。
车身材料的碳纤维
碳纤维是一种力学性能优异的新材料,它的比重不到钢的1/4,抗拉强度却达到钢的7-9倍,以其制造的汽车可以节约燃油30%。碳纤维最初只应用于军事、航空航天等高科技领域,目前汽车界对碳纤维的利用已经趋于成熟。
目前,碳纤维已经应用到了汽车的各个部分,比如车身,车顶,后备箱盖,刹车盘,内饰部分,等等。
代表车型:宝马M3
碳纤维材料在bmw M3上的应用有利于降低车辆重心,减少能耗并进一步提升本以达到极致的驾驶体验,是BMWM的轻量化设计哲学的最新成就,充分体现出BMW M对完美境界的不懈追求。
宝马公司特别为中国提供111辆BMWM3碳纤限量版。除了装备碳纤维车顶,还在前保险杠下面的裙边、后扰流板以及内饰等部位使用碳纤维材质,让卓尔不群的M3更加珍贵而富有个性。
阻碍碳纤维在汽车领域商品化的关键因素是制造成本。不过,随着碳纤维行业的不断成熟与发展,以及节能减排和汽车轻量化大方向的指引,碳纤维材料或成汽车界“瘦身革命”的领导者。可以预见,碳纤维轻量车身必将掀起一股新的变革潮流,一个新的市场突破点正在形成。
NO.2 新型塑料更多的使用在零件上
汽车的轻量化可以通过换用强度更高、质量更轻的金属材料来实现。塑料及其复合材料可以减轻零件约40%的质量,而且可以使采购承办降低40%,发达国家车用塑料已占塑料消耗总量的7%~11%。而对于塑料零件来说,最难的是如何在减轻其重量的同时还能保持其强度、耐用性或性能不变。
现在,福特发现了解决这一难题的方法,通过采用在零件成型过程中充入气泡的方式,形成极为细微的蜂巢状结构,这些细微的空隙既节约了塑材,又减轻了重量,而且不会影响零件的任何性能。
与普通的工艺流程相比,MuCell技术可降低注塑成型过程中所需的压力,实现生产效率提升33%,从而降低制造的能耗、排放和成本。
2011-2012车展期间,巴斯夫、陶氏、杜邦等化工巨头带来了汽车相关的解决方案。不管最终采用哪种方案,目的都是要让汽车减轻体重、有效节能。对于化工企业来说,对材料进行改进是最好的办法,在保证结构强度的同时可以尽可能降低自身重量。更多的技术设计机构和企业巨头投入到了研究新型轻型环保材料的领域。
汽车的轻量化,不仅包括减轻车身的重量,还涉及对车身结构的整合,重新设计,达到最佳的轻量效果。在保证汽车的强度和安全性能的前提下,尽可能地降低汽车的整备质量,从而提高汽车的动力性,减少燃料消耗,降低排气污染。实验证明,若汽车整车重量降低10%,燃油效率可提高6%—8%;汽车整备质量每减少100公斤,百公里油耗可降低0.3—0.6升;汽车重量降低1%,油耗可降低0.7%。
轻量化的车身设计,要求车身结构更加合理,车内空间也会更大。缩小尺寸的汽车还可以节省物料的使用,应用新型材料使车身变轻以后使车辆行驶更加快速,节能。
NO.1 碳纤维作为汽车新兴材料的出现,大大减轻了汽车的重量
碳纤维用在一体式车架
这种一体式车架,早期用在飞机火箭上,后来被f1赛车成功推广,被称作单体壳,至此在跑车界蔓延开来。碳纤维的承载式车身能承受更大的拉应力,在目前的极速范围内,这个封闭的座舱,能够在车身在高速冲撞,车体彻底支解后,保证驾驶者的绝对安全。
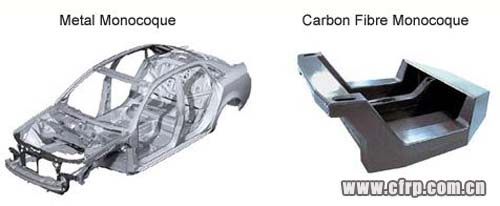
碳纤维复合材质车架
从图中我们可以看出,左边的金属车架和右边的碳纤维车架差别明显,碳纤维车架不同于传统的焊接或者铆接技术,结合新材料的特点和制造工艺,我们所看到的碳纤维车身都像盒子一样,和普通的承载式车身的区别还是很大。
代表车型:兰博基尼AventadorLP700-4
这款兰博基尼旗舰款超级跑车颇具未来风格,车舱完全以碳纤维制造而成,并配以硬壳式结构。其承载结构则为“单壳体”设计,在构造上可作为单一部件发挥作用,从而充分利用碳纤维强化材料的超强刚度。
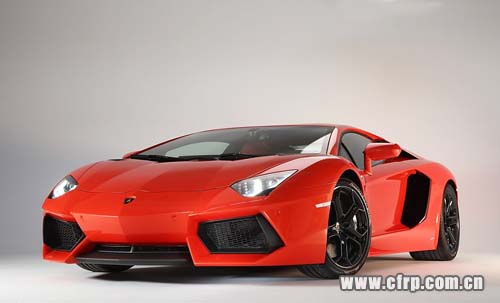
当然,“单壳体”的称谓只是一种形容,新型兰博基尼硬壳式车体其实是由一系列功能各异的独立部件构造而成,运用“编织”(Braiding)技术制成的加强件就是其一。“编织”是业内最有效的碰撞能量吸收技术之一。尽管是由众多部件集合而成,但经过固化之后,这种结构就能化为单一部件统一工作,底部结构称为“骨架”,与整个车顶都囊括在其中。并且,该车全硬壳式结构重量仅有145.5公斤(324.5磅)。
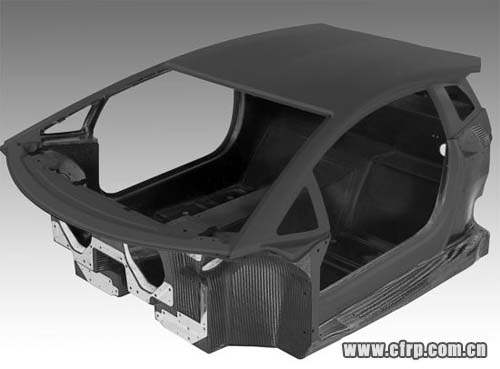
兰博基尼AventadorLP700-4 碳纤维一体车架
虽然一体式碳纤维车架很坚韧,但有受力向度的问题,即整体中的某些部位不太能受力。每辆车都根据自己整体的情况特别设计车架,如F50的车架将后悬架直接连接在发动机及变速器上,再将整个发动机悬架结构嵌入车体内,其车架只重102kg,而抗扭度高达3550kgm/degree。这种设计可以营造极轻量的悬架重量,但同时会有较大的发动机振荡传入车厢。
但是碳纤维不适合做越野车车架,因为越野车车架通常都需要允许非常大的变形和扭动等。目前的碳纤维太过于脆,没有良好的韧性。
车身材料的碳纤维
碳纤维是一种力学性能优异的新材料,它的比重不到钢的1/4,抗拉强度却达到钢的7-9倍,以其制造的汽车可以节约燃油30%。碳纤维最初只应用于军事、航空航天等高科技领域,目前汽车界对碳纤维的利用已经趋于成熟。
目前,碳纤维已经应用到了汽车的各个部分,比如车身,车顶,后备箱盖,刹车盘,内饰部分,等等。
代表车型:宝马M3
碳纤维材料在bmw M3上的应用有利于降低车辆重心,减少能耗并进一步提升本以达到极致的驾驶体验,是BMWM的轻量化设计哲学的最新成就,充分体现出BMW M对完美境界的不懈追求。

宝马公司特别为中国提供111辆BMWM3碳纤限量版。除了装备碳纤维车顶,还在前保险杠下面的裙边、后扰流板以及内饰等部位使用碳纤维材质,让卓尔不群的M3更加珍贵而富有个性。
阻碍碳纤维在汽车领域商品化的关键因素是制造成本。不过,随着碳纤维行业的不断成熟与发展,以及节能减排和汽车轻量化大方向的指引,碳纤维材料或成汽车界“瘦身革命”的领导者。可以预见,碳纤维轻量车身必将掀起一股新的变革潮流,一个新的市场突破点正在形成。
NO.2 新型塑料更多的使用在零件上
汽车的轻量化可以通过换用强度更高、质量更轻的金属材料来实现。塑料及其复合材料可以减轻零件约40%的质量,而且可以使采购承办降低40%,发达国家车用塑料已占塑料消耗总量的7%~11%。而对于塑料零件来说,最难的是如何在减轻其重量的同时还能保持其强度、耐用性或性能不变。
现在,福特发现了解决这一难题的方法,通过采用在零件成型过程中充入气泡的方式,形成极为细微的蜂巢状结构,这些细微的空隙既节约了塑材,又减轻了重量,而且不会影响零件的任何性能。

与普通的工艺流程相比,MuCell技术可降低注塑成型过程中所需的压力,实现生产效率提升33%,从而降低制造的能耗、排放和成本。
2011-2012车展期间,巴斯夫、陶氏、杜邦等化工巨头带来了汽车相关的解决方案。不管最终采用哪种方案,目的都是要让汽车减轻体重、有效节能。对于化工企业来说,对材料进行改进是最好的办法,在保证结构强度的同时可以尽可能降低自身重量。更多的技术设计机构和企业巨头投入到了研究新型轻型环保材料的领域。