热塑性树脂碳纤维复合材料或成突破量产难关杀手锏
By www.carbonfiber.com.cn
热塑性树脂碳纤维复合材料或成突破量产难关杀手锏
作为2008年度~2012年度的五年计划,日本新能源产业技术综合开发机构(NEDO)实施了产学合作项目“以碳纤维复合材料实现低能耗、循环型社会”。
该项目是从全球气候变暖对策的角度出发,针对汽车车身用途,研发采用碳纤维的新材料。参加该项目的,包括咨询委员会在内,有东丽、三菱丽阳、东洋纺、东京大学、东北大学、京都工艺纤维大学等11家企业和大学。力争通过将原来的铁换成这种新材料,使车身重量减轻30%。
“如果电动汽车(EV)与用碳纤维相结合,日本的汽车产业将如虎添翼”,东京大学工学系研究科教授高桥淳如是说。
东京大学工学系研究科系统创建学专业教授高桥淳
高桥教授在2008~2012财年以五年计划实施的日本新能源产业技术综合开发机构(NEDO)产学合作项目“以碳纤维复合材料实现低能耗、循环型社会”中担任项目负责人。
该项目是从全球气候变暖对策的角度出发,针对汽车车身用途,研发采用碳纤维的新材料。参加该项目的,包括咨询委员会在内,有东丽、三菱丽阳、东洋纺、东京大学、东北大学、京都工艺纤维大学等11家企业和大学,力争通过将原来的铁换成这种新材料,使车身重量减轻30%。
减轻车身重量从提高燃效的角度来说,是非常重要的。
高桥教授说:“虽然减轻汽油车的重量也非常重要,但对于日本来说,比其具有更大意义的是减轻电动汽车、混合动力车(HEV)及插电式混合动力车(PHEV)的重量。”
Meeting with New Energy and Industrial Technology Development Organization (NEDO).
目前,电动汽车和混合动力车正逐步得到普及。在这里成为课题的是充电电池。据预测今后在电动汽车和混合动力车配备的充电电池领域,锂离子电池将成为主流。不过,锂属于“稀有金属”,原料主要依赖进口。价格较高,目前已经成为阻碍电动汽车、混合动力车降低价格的重要原因。
并且,充电时间也是一个较大的课题。例如,三菱汽车的电动汽车“i-MiEV”,利用普通家用电源,8小时以上才能充满电。
不过,如果通过减轻车身重量来提高燃效,既能实现电池小型化,也能降低电动汽车和混合动力车的价格,并推动其进一步普及。还可降低对中国的依赖程度,缩短充电时间。充电电池的许多相关课题将得到解决。
高桥教授强调:“能够实现车身轻量化的,唯有日本具有绝对国际竞争力的碳纤维。”
不适合大量生产的原有复合材料
碳纤维是大约50年前由日本人发明的材料。其最大的魅力在于重量轻而强度高。尽管重量只有铁的4分之1,但强度为铁的10倍。而且不会生锈。
因此,作为实现低碳社会的重要王牌之一,受到了全球的关注。比如,为了提高燃效,利用塑料树脂凝固了碳纤维的“碳纤维复合材料(CFRP=carbon fiber reinforced plastics)”被应用于最新型飞机“波音787”的机身等。
截至2010年,碳纤维全球份额的7成左右由东丽(34%)、东邦特耐克丝集团(19%)及三菱丽阳集团(16%)占据,是日本国际竞争力最强的产业领域之一。
虽然统称碳纤维,但品质和用途也各种各样,特别是应用于波音787的碳纤维,是东丽花费40多年时间研发出来的汗水和泪水的结晶。
“因此,虽然目前美国和中国也出现了致力于碳纤维开发的企业,但我认为其他国家在品质方面很难赶上日本”,高桥教授对此满怀自信。
由于重量轻而且具有高强度,因此实际上不仅是客机,碳纤维复合材料也已经被应用于国际“F1”车赛的赛车车身、风力发电风车的一部分、钓竿及网球拍等多个领域。
不过,先不说电动汽车和混合动力车,此前连汽油车都未加以采用的原因何在?。
其原因就在于,现有碳纤维复合材料无法进行大量生产。因此,项目的目的就在于开发出可大量生产的碳纤维复合材料。
现有碳纤维复合材料除了不能进行大量生产之外,还有价格高、不能循环再利用等课题。这些课题实际上均来自现在使用的塑料树脂的特性。项目要力争解决上述所有课题。
在“热可塑性”树脂上寻找出路
在碳纤维复合材料中,主要使用的是名为“环氧树脂”的“热固性”塑料树脂。热固性树脂是指一旦加热凝固之后,即使再次加热也无法恢复原先状态的树脂。其代表例子就是瞬间粘合剂。
现有碳纤维复合材料是将1万多根直径为7微米(微为100万分之1)的碳纤维集结成束,使之方向一致地排列整齐,然后含浸液态热固性树脂,利用热使树脂凝固制造而成的。
要使热固性树脂保持一定的强度,需要花费时间。这是因为,通过使之缓慢地发生化学反应,分子结构会变得整齐,形成更加坚固的材料。例如,波音787使用的材料是用4个多小时的时间凝固成形的。这是无法实现大量生产的最大原因。
高桥教授说道:“东丽宣布开发出了可在10分钟内成形的碳纤维复合材料,但要使用碳纤维复合材料量产车身,这还远远不够。必须能够在1分钟内成形。”
而且,不能进行循环再利用也是一个很大的课题。现在,汽车生产线的车身制造流程是使用模具将铁板冲压成形,再进行焊接。冲压后的残留部分等进行循环再利用。
不过,如果是碳纤维复合材料,残留部分只能废弃。这是因为,已经凝固的树脂无法像铁一样熔化并进行再利用。因此,据称作为材料使用的碳纤维复合材料会有接近一半被废弃。
另外,成形前必须进行冷冻保存等,这也花费不少成本,因此,现在碳纤维复合材料的价格高达1公斤1万日元以上。而铁每公斤仅为几百日元,价格相差两位数。
因此,高桥教授等致力于实现使用比较容易加工的“热可塑性树脂”的碳纤维复合材料的实用化。
热可塑性树脂是指凝固之后,如果再次加热可重新成形的树脂。受热会变软的塑料布和塑料盒就是用热可塑性树脂制成的。热可塑性树脂仅需一分钟时间即可成形。
在强度相同的情况下,车身重量可减轻30%
实际上,此前也曾多次对开发使用热可塑性树脂的碳纤维复合材料进行研究,不过并未成功。究其原因,主要是因为无法使热可塑性树脂和碳纤维很好地粘合在一起。
因此,项目分别对碳纤维和热可塑性树脂进行了改进。碳纤维由东丽和三菱丽阳负责,热可塑性树脂由东洋纺负责。
经过各企业的努力,终于实现了符合要求的粘合性和含浸性。成功使车身重量减轻了30%,同时还确保了与热固性树脂碳纤维复合材料同等的强度。
高桥教授回顾道:“虽然与技术相关的详细内容不便透露,但使用热可塑性树脂的碳纤维复合材料的突破点,就在于粘合性和含浸性。”
热可塑性树脂碳纤维复合材料中碳纤维的长度,不分用途均在1厘米以下。根根方向不一,重叠分布于树脂之中。
由于本来就比较短,因此即使利用冲压机切割掉不需要的部分,也很少因切割导致强度下降。接近100%可进行循环再利用,因此经济效益也得到大幅提升。也无需用于冷冻保存的大规模设备费及运用费。
“全球每年生产5000万辆车辆。我的梦想就是,使这些车辆的车身全部换用热可塑性树脂碳纤维复合材料”,高桥教授雄心勃勃地说道。
该项目是在174公斤碳纤维复合材料中加入100公斤碳纤维。假设一辆车使用100公斤的碳纤维,那么每年有望需要500万吨碳纤维。
不过,目前碳纤维的全球年产能仅为6万吨。因此,日本新能源产业技术综合开发机构还在同时推进旨在实现如今10倍年产量的项目。另外,碳纤维目前的价格高达每公斤3000日元左右,但据高桥教授计算,如果产能提高到目前的10倍,价格便可降低到每公斤1000日元左右。
如果热可塑性树脂碳纤维复合材料实现实用化,得到广泛普及,便可实现更加环保、人性化及节约成本的汽车社会。据称通过该项目,2016~18年实现实用化已有头绪。希望能够早日投入实用。
Teruhiro Sakurai, New Energy and Industrial Technology Development Organization (NEDO), Japan
热塑性树脂碳纤维复合材料或成突破量产难关杀手锏
作为2008年度~2012年度的五年计划,日本新能源产业技术综合开发机构(NEDO)实施了产学合作项目“以碳纤维复合材料实现低能耗、循环型社会”。
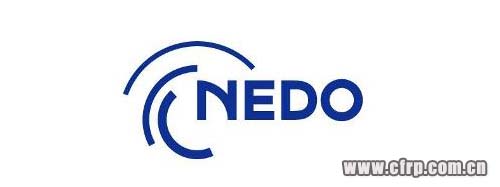
该项目是从全球气候变暖对策的角度出发,针对汽车车身用途,研发采用碳纤维的新材料。参加该项目的,包括咨询委员会在内,有东丽、三菱丽阳、东洋纺、东京大学、东北大学、京都工艺纤维大学等11家企业和大学。力争通过将原来的铁换成这种新材料,使车身重量减轻30%。
“如果电动汽车(EV)与用碳纤维相结合,日本的汽车产业将如虎添翼”,东京大学工学系研究科教授高桥淳如是说。

东京大学工学系研究科系统创建学专业教授高桥淳
高桥教授在2008~2012财年以五年计划实施的日本新能源产业技术综合开发机构(NEDO)产学合作项目“以碳纤维复合材料实现低能耗、循环型社会”中担任项目负责人。
该项目是从全球气候变暖对策的角度出发,针对汽车车身用途,研发采用碳纤维的新材料。参加该项目的,包括咨询委员会在内,有东丽、三菱丽阳、东洋纺、东京大学、东北大学、京都工艺纤维大学等11家企业和大学,力争通过将原来的铁换成这种新材料,使车身重量减轻30%。
减轻车身重量从提高燃效的角度来说,是非常重要的。
高桥教授说:“虽然减轻汽油车的重量也非常重要,但对于日本来说,比其具有更大意义的是减轻电动汽车、混合动力车(HEV)及插电式混合动力车(PHEV)的重量。”

Meeting with New Energy and Industrial Technology Development Organization (NEDO).
目前,电动汽车和混合动力车正逐步得到普及。在这里成为课题的是充电电池。据预测今后在电动汽车和混合动力车配备的充电电池领域,锂离子电池将成为主流。不过,锂属于“稀有金属”,原料主要依赖进口。价格较高,目前已经成为阻碍电动汽车、混合动力车降低价格的重要原因。
并且,充电时间也是一个较大的课题。例如,三菱汽车的电动汽车“i-MiEV”,利用普通家用电源,8小时以上才能充满电。
不过,如果通过减轻车身重量来提高燃效,既能实现电池小型化,也能降低电动汽车和混合动力车的价格,并推动其进一步普及。还可降低对中国的依赖程度,缩短充电时间。充电电池的许多相关课题将得到解决。
高桥教授强调:“能够实现车身轻量化的,唯有日本具有绝对国际竞争力的碳纤维。”
不适合大量生产的原有复合材料
碳纤维是大约50年前由日本人发明的材料。其最大的魅力在于重量轻而强度高。尽管重量只有铁的4分之1,但强度为铁的10倍。而且不会生锈。
因此,作为实现低碳社会的重要王牌之一,受到了全球的关注。比如,为了提高燃效,利用塑料树脂凝固了碳纤维的“碳纤维复合材料(CFRP=carbon fiber reinforced plastics)”被应用于最新型飞机“波音787”的机身等。
截至2010年,碳纤维全球份额的7成左右由东丽(34%)、东邦特耐克丝集团(19%)及三菱丽阳集团(16%)占据,是日本国际竞争力最强的产业领域之一。
虽然统称碳纤维,但品质和用途也各种各样,特别是应用于波音787的碳纤维,是东丽花费40多年时间研发出来的汗水和泪水的结晶。
“因此,虽然目前美国和中国也出现了致力于碳纤维开发的企业,但我认为其他国家在品质方面很难赶上日本”,高桥教授对此满怀自信。
由于重量轻而且具有高强度,因此实际上不仅是客机,碳纤维复合材料也已经被应用于国际“F1”车赛的赛车车身、风力发电风车的一部分、钓竿及网球拍等多个领域。
不过,先不说电动汽车和混合动力车,此前连汽油车都未加以采用的原因何在?。
其原因就在于,现有碳纤维复合材料无法进行大量生产。因此,项目的目的就在于开发出可大量生产的碳纤维复合材料。
现有碳纤维复合材料除了不能进行大量生产之外,还有价格高、不能循环再利用等课题。这些课题实际上均来自现在使用的塑料树脂的特性。项目要力争解决上述所有课题。
在“热可塑性”树脂上寻找出路
在碳纤维复合材料中,主要使用的是名为“环氧树脂”的“热固性”塑料树脂。热固性树脂是指一旦加热凝固之后,即使再次加热也无法恢复原先状态的树脂。其代表例子就是瞬间粘合剂。
现有碳纤维复合材料是将1万多根直径为7微米(微为100万分之1)的碳纤维集结成束,使之方向一致地排列整齐,然后含浸液态热固性树脂,利用热使树脂凝固制造而成的。
要使热固性树脂保持一定的强度,需要花费时间。这是因为,通过使之缓慢地发生化学反应,分子结构会变得整齐,形成更加坚固的材料。例如,波音787使用的材料是用4个多小时的时间凝固成形的。这是无法实现大量生产的最大原因。
高桥教授说道:“东丽宣布开发出了可在10分钟内成形的碳纤维复合材料,但要使用碳纤维复合材料量产车身,这还远远不够。必须能够在1分钟内成形。”
而且,不能进行循环再利用也是一个很大的课题。现在,汽车生产线的车身制造流程是使用模具将铁板冲压成形,再进行焊接。冲压后的残留部分等进行循环再利用。
不过,如果是碳纤维复合材料,残留部分只能废弃。这是因为,已经凝固的树脂无法像铁一样熔化并进行再利用。因此,据称作为材料使用的碳纤维复合材料会有接近一半被废弃。
另外,成形前必须进行冷冻保存等,这也花费不少成本,因此,现在碳纤维复合材料的价格高达1公斤1万日元以上。而铁每公斤仅为几百日元,价格相差两位数。
因此,高桥教授等致力于实现使用比较容易加工的“热可塑性树脂”的碳纤维复合材料的实用化。
热可塑性树脂是指凝固之后,如果再次加热可重新成形的树脂。受热会变软的塑料布和塑料盒就是用热可塑性树脂制成的。热可塑性树脂仅需一分钟时间即可成形。
在强度相同的情况下,车身重量可减轻30%
实际上,此前也曾多次对开发使用热可塑性树脂的碳纤维复合材料进行研究,不过并未成功。究其原因,主要是因为无法使热可塑性树脂和碳纤维很好地粘合在一起。
因此,项目分别对碳纤维和热可塑性树脂进行了改进。碳纤维由东丽和三菱丽阳负责,热可塑性树脂由东洋纺负责。
经过各企业的努力,终于实现了符合要求的粘合性和含浸性。成功使车身重量减轻了30%,同时还确保了与热固性树脂碳纤维复合材料同等的强度。
高桥教授回顾道:“虽然与技术相关的详细内容不便透露,但使用热可塑性树脂的碳纤维复合材料的突破点,就在于粘合性和含浸性。”
热可塑性树脂碳纤维复合材料中碳纤维的长度,不分用途均在1厘米以下。根根方向不一,重叠分布于树脂之中。
由于本来就比较短,因此即使利用冲压机切割掉不需要的部分,也很少因切割导致强度下降。接近100%可进行循环再利用,因此经济效益也得到大幅提升。也无需用于冷冻保存的大规模设备费及运用费。
“全球每年生产5000万辆车辆。我的梦想就是,使这些车辆的车身全部换用热可塑性树脂碳纤维复合材料”,高桥教授雄心勃勃地说道。
该项目是在174公斤碳纤维复合材料中加入100公斤碳纤维。假设一辆车使用100公斤的碳纤维,那么每年有望需要500万吨碳纤维。
不过,目前碳纤维的全球年产能仅为6万吨。因此,日本新能源产业技术综合开发机构还在同时推进旨在实现如今10倍年产量的项目。另外,碳纤维目前的价格高达每公斤3000日元左右,但据高桥教授计算,如果产能提高到目前的10倍,价格便可降低到每公斤1000日元左右。
如果热可塑性树脂碳纤维复合材料实现实用化,得到广泛普及,便可实现更加环保、人性化及节约成本的汽车社会。据称通过该项目,2016~18年实现实用化已有头绪。希望能够早日投入实用。
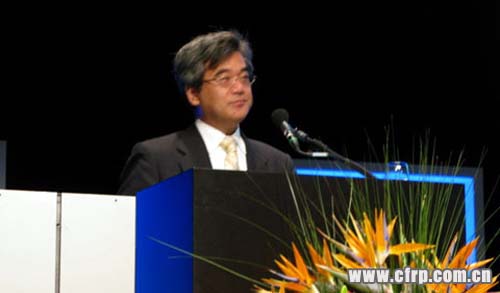
Teruhiro Sakurai, New Energy and Industrial Technology Development Organization (NEDO), Japan