复合材料热压罐成型模具设计研究
By www.carbonfiber.com.cn
随着复合材料在飞机结构件上用量的逐步增加,零件越来越大而复杂,并逐步使用到主承力件上,这对复合材料制件的质量提出了更高的要求。因复合材料制件的固化成型特点,其质量在很大程度上取决于成型模具的质量,而高质量的模具来源于科学、合理的设计,特别是对于大型模具,除模具质量对制件质量的影响外,模具的尺寸、重量对模具成本以及复材制件的总制造成本有很大影响。
通过对复合材料热压罐成型模具的设计、制造、转运及使用验证等工程研究及分析,结合复材模具设计的经验方法,归纳出以下几点模具设计原则。
满足制件结构及工艺要求
在设计复合材料成型模具前,要对制件的设计输入进行充分分析,以产生模具结构的初步概念。
(1)分析制件的工程结构。通常有壁板、梁、肋、长桁、接头、以及整体盒段等结构形式。根据制件结构形式,可对模具有个大致概念,壁板常为大型框架结构;梁一般较长,常有阴模、阳模形式(图1、图2);长桁一般为细长结构;整体盒段一般需上下合模。
(2)分析制件的工程界面。是否有气动面、装配面、胶接面等,一般情况下可确定这些面为贴膜面;但如果这些面结构较复杂时,设计可考虑在工程界面侧添加补偿层,此时贴膜面可设计在工程界面的背面。
(3)分析制件的质量要求。制件的外形轮廓尺寸精度直接影响到模具的质量要求及成本,可通过设计合理的模具结构、定位方法及加工方法来达到精度要求。
(4)分析制件的成型工艺方法,是共固化、共胶接还是二次交接(图3)。共固化中,所有层为湿铺层一次进罐,需要较多模具组合到一起同时使用,通常整套模具较复杂;共胶接为干湿件进罐固化,需要一部分零件的成型模具,及已固化零件与湿铺层二次进罐固化的模具;二次胶接时所有零件已固化,通过胶膜把他们固化到一起,需要所有零件的成型模以及二次胶接的定位模具。
(图3)制件的成型工艺方法
模具材料的选择
用作复合材料成型模具的材料主要有普通钢、INVAR钢、复合材料(双马和环氧树脂)、铝等。通常根据材料的性能(主要是高温下的热膨胀系数)、成本、周期及使用次数来选择,见表1。
对于机身、翼面、舵面等大尺寸、大曲率的模具,通常选择INVAR钢,对于一些配合要求高的梁、肋、长桁等也常选择INVAR钢;对于铺丝需要回转的工装,考虑到重量因素,复合材料模具是一个不错的选择;对于形状不是太复杂、曲率很小或是等截面的制件结构,通常选择普通钢或铝以降低成本,但膨胀和变形因素需要在设计时得到补偿。不同模具材料的性能特点及使用范围如表1所示。
模具热膨胀的补偿
当模具与预浸料进热压罐固化时,随着温度的升高,模具会膨胀而使尺寸增大,达到保温状态时最大,此时预浸料反应固化,与模具尺寸一致。在固化完成后降温的过程中,模具和固化好的制件都会收缩,但如果模具材料与复合材料制件的热膨胀系数不一致,收缩量也就不一致,从而导致制件尺寸和模具尺寸有偏差。根据表1中材料的热膨胀系数,INVAR钢和复合材料模具受热膨胀对制件的影响很小,可忽略不计;但普通钢和铝则有影响,特别是当尺寸大时,必须要考虑膨胀量,否则产品尺寸会随模具的膨胀而偏大。
模具热膨胀可采取一定的补偿方法,按经验公式及试验验证,以制件质心为中心,把整个制件按如下纠正系数缩小,在模具设计时按照缩小后的制件作为工程输入。
F=1/[(T-P)×△T+1],式中,F为热膨胀纠正系数;T为模具的热膨胀系数;P为复合材料制件的热膨胀系数;△T为固化温度和室温的差值。
另一方面,模具热膨胀还将影响到制件的变形及脱模等问题。在设计模具时要把这些因素考虑进去。如收缩变形是否能通过模具结构的对称性来抵消,或后处理来消除;凸模的收缩可能会有助于脱模,特别是对于有微小闭角的零件,凹模的收缩将增加脱模的难度。通过考虑这些因素,结合复材制件的产品要求,来选择合适的模具材料及模具的结构形式。同时,也可以通过数字模拟,结合试验件的验证来优化模具设计。
模具回弹角的补偿
除模具的膨胀对制件固化变形有影响外,复合材料制件因为铺层和结构的不对称性,以及材料本身的固化特性,在固化时产生内应力也将引起制件变形。而对于梁、长桁类有大夹角的零件,固化变形最显著的是回弹角,即制件在固化脱模后,夹角因收缩而小于模具角度,此差值为回弹角。如图4所示,A1为模具夹角,A2为制件脱模后的夹角,θ为二者之差,即回弹角。在设计时,不考虑回弹角或考虑不当,将对制件质量产生较大影响,特别是对装配的影响。
回弹角因与模具材料,铺层方向及结构对称性有关,可通过数字模拟及试验测试的方法得到,目前用的较多的是通过经验值结合试验值来获得回弹角的大小,而数字模拟有待于提高对热压罐温度场及复合材料反应机理的精准分析。在模具设计时,预先把回弹角考虑进去,即制件夹角加上回弹角等于模具夹角,使制件在脱模回弹后符合工程数模要求。
应力分析准则
目前国内的复合材料成型模具一般都是通过保守估计的方法设计,没有通过强度分析优化,这样设计出来的模具,特别是大型制件的模具,通常都非常笨重,不仅耗费大量材料,因热容量升高也可能影响到固化反应,同时对运输、使用过程的相关设备吨位要求很高,大大增加了成本,甚至影响了制造能力。因此,减重是模具设计优化的一个重要方面。减重的方法必须要通过合理的计算,否则会直接影响到模具的强度和刚度,导致使用过程中产生变形而影响制件质量。同时,对于吊环、轮子、撑脚也需要进行强度校核,以确保模具能够安全地起吊和转运。
减重优化可通过有限元分析模具在不同工况下的应变、应力情况(图5、图6),根据计算结果调整优化模具结构,最终使最严重工况下的应力、应变值小于材料许用值乘以某一安全系数(此安全系数一般为经验值,为安全起见,可考虑大于1.5),并尽可能使各处的安全系数偏差不大,这样才能有效减重。模具应力分析考虑的工况通常包括以下几个方面:
图5 应变分析
图6 应力分析
(1) 垂直起吊的情况。
整套模具加制件的重量作用在模具的所有吊点上。
(2) 垂直起吊过程紧急刹车情况。
整套模具加制件的重量,以及急刹车产生的冲击载荷作用在模具的所有吊点上。
(3) 手动铺层使用情况。
铺贴模具加铺层重量作用在模具底座的支撑点上。
(4) 自动铺层使用情况。
铺贴模具加铺层重量,以及铺带头的压力作用在模具底座的支撑点上。
(5)工装转运过程。
整套模具加制件的重量作用在模具的轮子上。
(6) 工装在热压罐里的情况。
在177℃时(此时的材料许用值小于常温下的许用值),整套模具加制件的重量作用在模具底座的支撑点上。
细节设计要求
复合材料模具设计中细节设计非常重要,直接影响到模具使用的可操作性、方便性及自动化程度,甚至影响复合材料制件的质量。模具上的细节设计(图7)包括但不限于以下内容:
(1) 产品线:即产品的外形轮廓线,用于非数控切边时使用,决定了产品的外形尺寸的精度;设计时应考虑模具材料的膨胀因素作适当缩放处理,产品线的位置精度和宽度精度都需要根据复材制件外形尺寸精度要求定义在模具设计中。
(2) 铺贴线:由于制件边缘铺贴不完全齐整,以及流胶、挡胶条、打真空袋等因素导致固化后产品边缘质量不高,需要在产品线外一定距离开始铺贴,在制件上将留有一定余量待加工掉。同时,铺贴线用于无激光投影时手工铺贴定位,以控制铺贴余量,既不浪费太多的料,又能保证产品质量。通常铺贴线到产品线可留20~30mm。
(3) 基准孔:用于模具机加和检测时作为基准,精度要高,并保证可重复使用。基准孔坐标值通常刻于模具上便于使用。
(4) 靶标孔:用于手动铺贴时放置激光投影的靶标,以定位铺层区域。靶标孔按实测值即可,坐标值刻于模具上。
(5) 自动铺带十字刻线:十字刻线中心用于自动铺带时目标定位,十字线中心点的坐标刻于模具上。
(6) 复材制件定位孔:也叫制件工艺耳片孔,用于复材制件在脱模后检测、机加和装配时作定位基准,精度要求高。此孔需要有相应的钻模板来准确定位,钻孔需要在脱模前进行,孔应该在模具的法线方向。
(7) 余量区:在铺贴线到模具边缘需要留有一定距离用于打真空袋及自动铺带退料。通常手工铺贴模具的余量区在100~200mm,而自动铺带则需要200~300mm。
(8) 人性化设计:模具设计时要考虑工装使用安全、便利,比如工装的高度要适于铺贴、检查;模具铺贴、搬运时要稳,不会有砸到的危险;当重量超过人工搬运的重量时,要设计辅助工装协助模具转运。
特大型模具的约束因素
复材成型模具通常都非常笨重,如尾翼、机翼、机身等制件成型模具,动则十几吨,甚至几十吨。如此大而重的模具,在制造、运输和使用过程中将大大增加难度。
设计过程:随着尺寸的增大,保证模具加工精度、热均匀性以及变形控制的难度将提高。在设计时,这些因素都应考虑到,如基准的设定、公差的分配,以及应力计算,还有目前正在研究的考虑到热压罐的温度场对模具热分布的影响等。
制造过程:要保证大型模具的制造精度、气密性等设计要求,对焊接、热处理、数控机加及检测技术等都提出了很高的要求,目前如激光焊接、氦气检漏等新工艺正逐步应用到大型模具的制造中。
运输过程:重量过大则对桥梁、路基有更高的要求;尺寸增大对关卡、收费站等宽度有要求,通常长宽均超过3.5m时将受限,而达到5m以上时,将要对整个运输道路进行考察,甚至改造。此情况下,需要考虑将模具分块制造,运输到制造现场以后进行焊接。
使用过程:对于大尺寸、大吨位的模具,通常需要在厂房规划和设备采购时就考虑转运空间、吊车吨位、设备行程等因素。
结束语
综上所述,模具设计不仅需要考虑工程、工艺输入,还需要考虑制造加工能力、运输、使用及相关设备能力等因素,使设计出的模具不仅能制造出合格的复材制件,还能达到降低成本、方便使用的更高目标。目前,减重、变形控制、人性化设计等是模具优化的发展方向,利用不断升级的设计工具,结合实践经验的积累,复材成型模具将会得到更好的优化,从而促进复合材料在航空领域的发展。(责编 夏宛)
作者:晏冬秀 刘卫平等
作者单位:上海飞机制造有限公司航研所
随着复合材料在飞机结构件上用量的逐步增加,零件越来越大而复杂,并逐步使用到主承力件上,这对复合材料制件的质量提出了更高的要求。因复合材料制件的固化成型特点,其质量在很大程度上取决于成型模具的质量,而高质量的模具来源于科学、合理的设计,特别是对于大型模具,除模具质量对制件质量的影响外,模具的尺寸、重量对模具成本以及复材制件的总制造成本有很大影响。
通过对复合材料热压罐成型模具的设计、制造、转运及使用验证等工程研究及分析,结合复材模具设计的经验方法,归纳出以下几点模具设计原则。
满足制件结构及工艺要求
在设计复合材料成型模具前,要对制件的设计输入进行充分分析,以产生模具结构的初步概念。
(1)分析制件的工程结构。通常有壁板、梁、肋、长桁、接头、以及整体盒段等结构形式。根据制件结构形式,可对模具有个大致概念,壁板常为大型框架结构;梁一般较长,常有阴模、阳模形式(图1、图2);长桁一般为细长结构;整体盒段一般需上下合模。
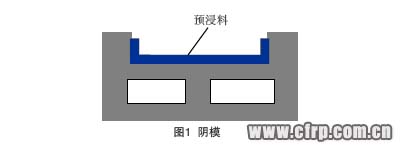
(2)分析制件的工程界面。是否有气动面、装配面、胶接面等,一般情况下可确定这些面为贴膜面;但如果这些面结构较复杂时,设计可考虑在工程界面侧添加补偿层,此时贴膜面可设计在工程界面的背面。
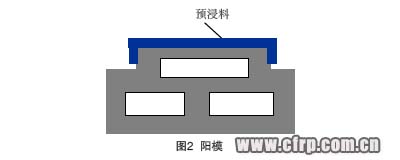
(3)分析制件的质量要求。制件的外形轮廓尺寸精度直接影响到模具的质量要求及成本,可通过设计合理的模具结构、定位方法及加工方法来达到精度要求。
(4)分析制件的成型工艺方法,是共固化、共胶接还是二次交接(图3)。共固化中,所有层为湿铺层一次进罐,需要较多模具组合到一起同时使用,通常整套模具较复杂;共胶接为干湿件进罐固化,需要一部分零件的成型模具,及已固化零件与湿铺层二次进罐固化的模具;二次胶接时所有零件已固化,通过胶膜把他们固化到一起,需要所有零件的成型模以及二次胶接的定位模具。

(图3)制件的成型工艺方法
模具材料的选择
用作复合材料成型模具的材料主要有普通钢、INVAR钢、复合材料(双马和环氧树脂)、铝等。通常根据材料的性能(主要是高温下的热膨胀系数)、成本、周期及使用次数来选择,见表1。

对于机身、翼面、舵面等大尺寸、大曲率的模具,通常选择INVAR钢,对于一些配合要求高的梁、肋、长桁等也常选择INVAR钢;对于铺丝需要回转的工装,考虑到重量因素,复合材料模具是一个不错的选择;对于形状不是太复杂、曲率很小或是等截面的制件结构,通常选择普通钢或铝以降低成本,但膨胀和变形因素需要在设计时得到补偿。不同模具材料的性能特点及使用范围如表1所示。
模具热膨胀的补偿
当模具与预浸料进热压罐固化时,随着温度的升高,模具会膨胀而使尺寸增大,达到保温状态时最大,此时预浸料反应固化,与模具尺寸一致。在固化完成后降温的过程中,模具和固化好的制件都会收缩,但如果模具材料与复合材料制件的热膨胀系数不一致,收缩量也就不一致,从而导致制件尺寸和模具尺寸有偏差。根据表1中材料的热膨胀系数,INVAR钢和复合材料模具受热膨胀对制件的影响很小,可忽略不计;但普通钢和铝则有影响,特别是当尺寸大时,必须要考虑膨胀量,否则产品尺寸会随模具的膨胀而偏大。
模具热膨胀可采取一定的补偿方法,按经验公式及试验验证,以制件质心为中心,把整个制件按如下纠正系数缩小,在模具设计时按照缩小后的制件作为工程输入。
F=1/[(T-P)×△T+1],式中,F为热膨胀纠正系数;T为模具的热膨胀系数;P为复合材料制件的热膨胀系数;△T为固化温度和室温的差值。
另一方面,模具热膨胀还将影响到制件的变形及脱模等问题。在设计模具时要把这些因素考虑进去。如收缩变形是否能通过模具结构的对称性来抵消,或后处理来消除;凸模的收缩可能会有助于脱模,特别是对于有微小闭角的零件,凹模的收缩将增加脱模的难度。通过考虑这些因素,结合复材制件的产品要求,来选择合适的模具材料及模具的结构形式。同时,也可以通过数字模拟,结合试验件的验证来优化模具设计。
模具回弹角的补偿
除模具的膨胀对制件固化变形有影响外,复合材料制件因为铺层和结构的不对称性,以及材料本身的固化特性,在固化时产生内应力也将引起制件变形。而对于梁、长桁类有大夹角的零件,固化变形最显著的是回弹角,即制件在固化脱模后,夹角因收缩而小于模具角度,此差值为回弹角。如图4所示,A1为模具夹角,A2为制件脱模后的夹角,θ为二者之差,即回弹角。在设计时,不考虑回弹角或考虑不当,将对制件质量产生较大影响,特别是对装配的影响。
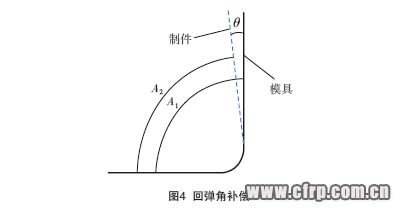
回弹角因与模具材料,铺层方向及结构对称性有关,可通过数字模拟及试验测试的方法得到,目前用的较多的是通过经验值结合试验值来获得回弹角的大小,而数字模拟有待于提高对热压罐温度场及复合材料反应机理的精准分析。在模具设计时,预先把回弹角考虑进去,即制件夹角加上回弹角等于模具夹角,使制件在脱模回弹后符合工程数模要求。
应力分析准则
目前国内的复合材料成型模具一般都是通过保守估计的方法设计,没有通过强度分析优化,这样设计出来的模具,特别是大型制件的模具,通常都非常笨重,不仅耗费大量材料,因热容量升高也可能影响到固化反应,同时对运输、使用过程的相关设备吨位要求很高,大大增加了成本,甚至影响了制造能力。因此,减重是模具设计优化的一个重要方面。减重的方法必须要通过合理的计算,否则会直接影响到模具的强度和刚度,导致使用过程中产生变形而影响制件质量。同时,对于吊环、轮子、撑脚也需要进行强度校核,以确保模具能够安全地起吊和转运。
减重优化可通过有限元分析模具在不同工况下的应变、应力情况(图5、图6),根据计算结果调整优化模具结构,最终使最严重工况下的应力、应变值小于材料许用值乘以某一安全系数(此安全系数一般为经验值,为安全起见,可考虑大于1.5),并尽可能使各处的安全系数偏差不大,这样才能有效减重。模具应力分析考虑的工况通常包括以下几个方面:

图5 应变分析

图6 应力分析
(1) 垂直起吊的情况。
整套模具加制件的重量作用在模具的所有吊点上。
(2) 垂直起吊过程紧急刹车情况。
整套模具加制件的重量,以及急刹车产生的冲击载荷作用在模具的所有吊点上。
(3) 手动铺层使用情况。
铺贴模具加铺层重量作用在模具底座的支撑点上。
(4) 自动铺层使用情况。
铺贴模具加铺层重量,以及铺带头的压力作用在模具底座的支撑点上。
(5)工装转运过程。
整套模具加制件的重量作用在模具的轮子上。
(6) 工装在热压罐里的情况。
在177℃时(此时的材料许用值小于常温下的许用值),整套模具加制件的重量作用在模具底座的支撑点上。
细节设计要求
复合材料模具设计中细节设计非常重要,直接影响到模具使用的可操作性、方便性及自动化程度,甚至影响复合材料制件的质量。模具上的细节设计(图7)包括但不限于以下内容:
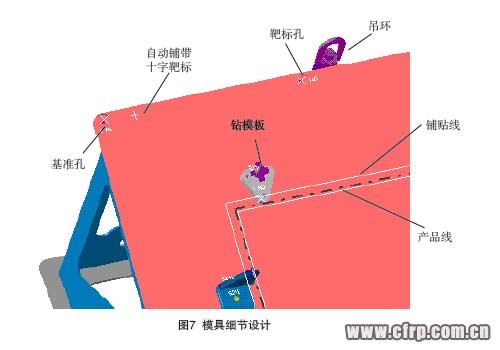
(1) 产品线:即产品的外形轮廓线,用于非数控切边时使用,决定了产品的外形尺寸的精度;设计时应考虑模具材料的膨胀因素作适当缩放处理,产品线的位置精度和宽度精度都需要根据复材制件外形尺寸精度要求定义在模具设计中。
(2) 铺贴线:由于制件边缘铺贴不完全齐整,以及流胶、挡胶条、打真空袋等因素导致固化后产品边缘质量不高,需要在产品线外一定距离开始铺贴,在制件上将留有一定余量待加工掉。同时,铺贴线用于无激光投影时手工铺贴定位,以控制铺贴余量,既不浪费太多的料,又能保证产品质量。通常铺贴线到产品线可留20~30mm。
(3) 基准孔:用于模具机加和检测时作为基准,精度要高,并保证可重复使用。基准孔坐标值通常刻于模具上便于使用。
(4) 靶标孔:用于手动铺贴时放置激光投影的靶标,以定位铺层区域。靶标孔按实测值即可,坐标值刻于模具上。
(5) 自动铺带十字刻线:十字刻线中心用于自动铺带时目标定位,十字线中心点的坐标刻于模具上。
(6) 复材制件定位孔:也叫制件工艺耳片孔,用于复材制件在脱模后检测、机加和装配时作定位基准,精度要求高。此孔需要有相应的钻模板来准确定位,钻孔需要在脱模前进行,孔应该在模具的法线方向。
(7) 余量区:在铺贴线到模具边缘需要留有一定距离用于打真空袋及自动铺带退料。通常手工铺贴模具的余量区在100~200mm,而自动铺带则需要200~300mm。
(8) 人性化设计:模具设计时要考虑工装使用安全、便利,比如工装的高度要适于铺贴、检查;模具铺贴、搬运时要稳,不会有砸到的危险;当重量超过人工搬运的重量时,要设计辅助工装协助模具转运。
特大型模具的约束因素
复材成型模具通常都非常笨重,如尾翼、机翼、机身等制件成型模具,动则十几吨,甚至几十吨。如此大而重的模具,在制造、运输和使用过程中将大大增加难度。
设计过程:随着尺寸的增大,保证模具加工精度、热均匀性以及变形控制的难度将提高。在设计时,这些因素都应考虑到,如基准的设定、公差的分配,以及应力计算,还有目前正在研究的考虑到热压罐的温度场对模具热分布的影响等。
制造过程:要保证大型模具的制造精度、气密性等设计要求,对焊接、热处理、数控机加及检测技术等都提出了很高的要求,目前如激光焊接、氦气检漏等新工艺正逐步应用到大型模具的制造中。
运输过程:重量过大则对桥梁、路基有更高的要求;尺寸增大对关卡、收费站等宽度有要求,通常长宽均超过3.5m时将受限,而达到5m以上时,将要对整个运输道路进行考察,甚至改造。此情况下,需要考虑将模具分块制造,运输到制造现场以后进行焊接。
使用过程:对于大尺寸、大吨位的模具,通常需要在厂房规划和设备采购时就考虑转运空间、吊车吨位、设备行程等因素。
结束语
综上所述,模具设计不仅需要考虑工程、工艺输入,还需要考虑制造加工能力、运输、使用及相关设备能力等因素,使设计出的模具不仅能制造出合格的复材制件,还能达到降低成本、方便使用的更高目标。目前,减重、变形控制、人性化设计等是模具优化的发展方向,利用不断升级的设计工具,结合实践经验的积累,复材成型模具将会得到更好的优化,从而促进复合材料在航空领域的发展。(责编 夏宛)
作者:晏冬秀 刘卫平等
作者单位:上海飞机制造有限公司航研所