碳纤维汽车节能减排
By www.carbonfiber.com.cn
碳纤维的应用,可以抵消电动汽车因配装电池组而增加的重量。使用碳纤维,有利于汽车节能减排,但由于种种原因,以前这种材料给人远在千里之外的感觉。随着“超大城市”上市日期日益临近,碳纤维正缓步走下神坛,逐步融入汽车制造领域。
日前在慕尼黑举办的“宝马创新日——未来汽车”活动中,Megacity(译为“超大城市”)电动汽车的外观设计效果图及关键模块部件首次曝光,该车计划2013年上市。“超大城市”的意义不仅在于它是高档品牌推出的电动汽车,更在于它将成为世界上第一款采用碳纤维车身的大批量量产车。
碳纤维的应用,可以抵消电动汽车因配装电池组而增加的重量。使用碳纤维,有利于汽车节能减排,但由于种种原因,以前这种材料给人远在千里之外的感觉。随着“超大城市”上市日期日益临近,碳纤维正缓步走下神坛,逐步融入汽车制造领域。
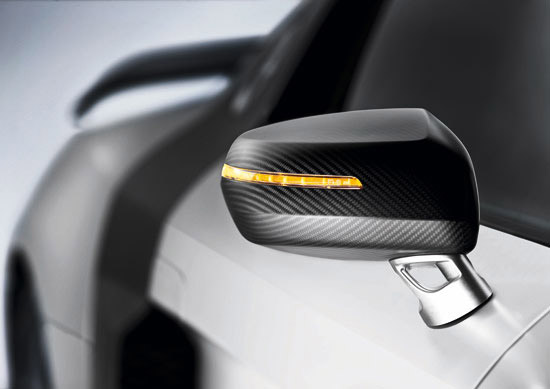
不再望碳纤维兴叹
汽车实现节能减排的路径较多,例如提高发动机的燃烧效率、使用清洁燃料和车载能源优化管理系统等,似乎“轻量化”这个传统、直接的手段不再受人们重视。自汽车诞生以来,工程师们就一直持续追求减轻车重,当然,这不完全出于节能的需要,还是提高车辆稳定性的要求。在没有找到合适的材料替代汽车用钢时,工程师们更多时候是在优化汽车结构或提高钢材的性能。
后来铝车身出现了,它明显轻于钢车身,很多高端车型甚至使用全铝车身。虽然铝还无法在普通车型上普及,但不可否认,它更适合制造汽车。不过铝也有弊端,包括原材料成本与加工成本过高、接合工艺较复杂等。要想成为汽车使用的主流材料,铝还需要弥补缺陷。
就在铝逐渐被广泛使用时,碳纤维闯入汽车界。碳纤维性能强、重量轻,广泛应用于航空航天领域。在汽车领域,由于使用成本高,碳纤维只在一级方程式赛车和某些超豪华品牌车辆上才能见到。到目前为止,几乎没有企业在批量生产的汽车上使用碳纤维,宝马是“第一个吃螃蟹”的。
汽车轻量化的新选择
即将投产的宝马“超大城市”电动汽车基本确定采用碳纤维车身。“超大城市”是宝马专为城市交通设计的电动汽车,体现该公司对电动汽车的前瞻研究成果。为了保证该车的竞争优势,宝马下了很大力气。“超级城市”主要有两个亮点,一是采用碳纤维整体车身,二是配装宝马自行研发的整合式底盘、电机和电池系统。
通常由于配装电池,电动汽车较普通内燃机汽车质量大。以MINI电动版为例,该车比同型号传统动力MINI重350公斤。较重的电动汽车需要更大电能来驱动,更大的电能又似乎需要更重的电池。终止这一“恶性循环”的措施之一,是大幅提高动力电池的能源密度,专家认为,这非常困难。另一个解决方案是大幅减轻电动汽车的自重,抵消因配装电池而增加的重量。宝马负责研发的董事克劳斯·德雷格说,“超大城市”开启汽车轻量化新篇章,通过使用碳纤维车身,该车基本与同级别内燃机汽车保持相同的整备质量。宝马称,到2013年,“超大城市”的重量将进一步减轻。
“碳纤维时代”已现曙光
碳纤维优点较多,但高昂的成本影响普及。宝马如何控制“超大城市”的成本?据了解,“超大城市”使用的碳纤维由欧洲最大碳纤维制造商SGL集团提供,宝马与该集团建立了合资公司,在美国生产碳纤维。以前SGL主要致力于研发、生产航空航天用碳纤维,此次宝马与其合作研发出汽车用碳纤维。据了解,这种纤维的成本可降到车企能接受的水平。今后,宝马计划将这种材料销售给其他汽车企业和飞机、风电设备制造商。
为了进一步降低成本,宝马专门研发了一套程序,可以重新合成碳纤维碎料,实现废物利用。这意味着“超大城市”报废后,该车使用的碳纤维可以回收再利用,降低材料报废的损失,从而降低成本。
随着技术和工艺不断成熟,碳纤维有望成为汽车业的主流材料。虽然实现这个目标还有很长的路要走,但随着“超大城市”接近量产,人们似乎看到了汽车业“碳纤维时代”的曙光。这不是宝马自己的事,关乎整个汽车业的节能减排大业。
先行一步是实现反牵制的砝码
在批量生产的车型上大量使用碳纤维材料,宝马“超大城市”电动汽车开了先河。碳纤维的优点令汽车工程师难以抗拒,碳纤维车身能比钢质车身减轻50%的重量,比铝车身轻约30%。同时,碳纤维不存在腐蚀生锈的问题,比普通金属耐用。在极端气候条件下,碳纤维的性质几乎不发生变化,这是金属材料很难实现的。使用碳纤维制造车身,可以省去高成本、繁琐的涂装工艺。难怪有人说,碳纤维几乎是目前可知的最能让汽车减重的完美材料。
笔者似乎一直在简单地说碳纤维的好话,其实由此联想到了深层问题———中国汽车业长期为铁矿石价格波动所困的境遇。目前要求中国钢铁企业联合起来,打破力拓、必何必拓与淡水河谷三大矿业巨头对铁矿石的价格垄断显然不现实,中国汽车企业要想在材料上不受制于人,笔者认为最好的方法是自己积极推进新材料研发。因此,碳纤维对于中国汽车来说,具有重要的意义。虽然碳纤维看似离中国汽车很远,但任何科技成果在成功使用前,都要经历漫长的改进过程。要想在未来及时实现突破,必须完成技术积累。在碳纤维使用方面,宝马已经给我们上了一课,我们应有为跨国公司“上课”的准备和信心。
奔驰SL系列将使用碳纤维零部件
戴姆勒日前宣布,与日本东丽集团合作研发的碳纤维零部件计划配装在2012年推出的新款奔驰SL系列车型上,这些零部件将在东丽位于法国的工厂生产。今年4月,双方决定成立合资公司,共同研发汽车碳纤维零部件。
据了解,碳纤维复合材料成形技术是由东丽首创的,此次与戴姆勒合作,是该公司首次研发汽车碳纤维零部件。东丽是世界最大碳纤维制造企业,产品占全球碳纤维市场34%的份额。此前,东丽曾为法拉利提供车用碳纤维。
戴姆勒与东丽的合作成果,结合两家企业的先进技术,有望大幅缩短碳纤维复合材料的成形周期。两家企业的共同目标是,计划未来3年为戴姆勒的奔驰SL系列车型研发出新型复合材料零部件。戴姆勒计划通过与东丽合作,将奔驰系列车型白车身的重量降低10%,以此提高车辆的燃油效率,减少有害气体排放。
1992年,通用汽车展出超轻概念车(Ultralite Concept Car)。该车车身由碳纤维复合材料制成,采用手铺碳纤维预浸料工艺制造。该车车身质量为191公斤,由于用碳纤维取代钢材制造车身和底盘部件,该车整备质量减轻68%,节油约40%。
旧飞机或将提供再生碳纤维
如今汽车行业已成功使用大量再生材料,如废钢铁和铝,能用来铸造新的车身架构;旧水瓶能变成车用塑料部件等。如今,汽车能用的再生材料又多了一个来源———退役战斗机。此前,再生碳纤维不能立即为汽车所用,除非出现能提供足够可用废料的载体。如今,退役战斗机也许能扮演这个角色,因此能提高它们的再利用水平。
20世纪70年代,碳纤维首先应用在军用飞机上。20世纪80年代,碳纤维在飞机上得到普遍使用,当时知名战斗机F-18大黄蜂的机翼,便使用了大量碳纤维。旧飞机是再生碳纤维的良好供应体,其提供的再生碳纤维能够取代新生产的碳纤维。退役战斗机的机翼一般由强度高、重量轻的碳纤维制成,回收的机翼等部件切碎后,可用于制造汽车碳纤维零部件。
IAC集团北美生产与验证中心工程总监韦恩·沃勒说:“尽管飞机用碳纤维要在其他领域实现再利用仍有困难,但这个设想为降低车用碳纤维的成本提供了解决方案。”
目前再生碳纤维的价格水平不得而知。据了解,工业级碳纤维的成本约为每磅(约合0.45公斤)10美元;航天级碳纤维每磅约25美元。IAC正在进行再生碳纤维的测试工作,如果证明使用来自飞机的再生碳纤维可行,那么再生碳纤维的价格可能随产量提高而下降。
F-18大黄蜂战斗机的机翼使用大量碳纤维。
今年3月,日本帝人集团发布了PU_PA超轻电动概念车,采用帝人独有材料制成,包括碳纤维复合材料、聚碳酸酯树脂和生物衍生聚酯。该车整备质量仅为437公斤。
碳纤维的应用,可以抵消电动汽车因配装电池组而增加的重量。使用碳纤维,有利于汽车节能减排,但由于种种原因,以前这种材料给人远在千里之外的感觉。随着“超大城市”上市日期日益临近,碳纤维正缓步走下神坛,逐步融入汽车制造领域。
日前在慕尼黑举办的“宝马创新日——未来汽车”活动中,Megacity(译为“超大城市”)电动汽车的外观设计效果图及关键模块部件首次曝光,该车计划2013年上市。“超大城市”的意义不仅在于它是高档品牌推出的电动汽车,更在于它将成为世界上第一款采用碳纤维车身的大批量量产车。
碳纤维的应用,可以抵消电动汽车因配装电池组而增加的重量。使用碳纤维,有利于汽车节能减排,但由于种种原因,以前这种材料给人远在千里之外的感觉。随着“超大城市”上市日期日益临近,碳纤维正缓步走下神坛,逐步融入汽车制造领域。
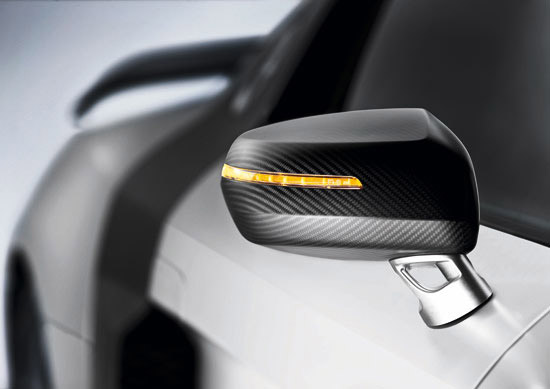
不再望碳纤维兴叹
汽车实现节能减排的路径较多,例如提高发动机的燃烧效率、使用清洁燃料和车载能源优化管理系统等,似乎“轻量化”这个传统、直接的手段不再受人们重视。自汽车诞生以来,工程师们就一直持续追求减轻车重,当然,这不完全出于节能的需要,还是提高车辆稳定性的要求。在没有找到合适的材料替代汽车用钢时,工程师们更多时候是在优化汽车结构或提高钢材的性能。
后来铝车身出现了,它明显轻于钢车身,很多高端车型甚至使用全铝车身。虽然铝还无法在普通车型上普及,但不可否认,它更适合制造汽车。不过铝也有弊端,包括原材料成本与加工成本过高、接合工艺较复杂等。要想成为汽车使用的主流材料,铝还需要弥补缺陷。
就在铝逐渐被广泛使用时,碳纤维闯入汽车界。碳纤维性能强、重量轻,广泛应用于航空航天领域。在汽车领域,由于使用成本高,碳纤维只在一级方程式赛车和某些超豪华品牌车辆上才能见到。到目前为止,几乎没有企业在批量生产的汽车上使用碳纤维,宝马是“第一个吃螃蟹”的。
汽车轻量化的新选择
即将投产的宝马“超大城市”电动汽车基本确定采用碳纤维车身。“超大城市”是宝马专为城市交通设计的电动汽车,体现该公司对电动汽车的前瞻研究成果。为了保证该车的竞争优势,宝马下了很大力气。“超级城市”主要有两个亮点,一是采用碳纤维整体车身,二是配装宝马自行研发的整合式底盘、电机和电池系统。
通常由于配装电池,电动汽车较普通内燃机汽车质量大。以MINI电动版为例,该车比同型号传统动力MINI重350公斤。较重的电动汽车需要更大电能来驱动,更大的电能又似乎需要更重的电池。终止这一“恶性循环”的措施之一,是大幅提高动力电池的能源密度,专家认为,这非常困难。另一个解决方案是大幅减轻电动汽车的自重,抵消因配装电池而增加的重量。宝马负责研发的董事克劳斯·德雷格说,“超大城市”开启汽车轻量化新篇章,通过使用碳纤维车身,该车基本与同级别内燃机汽车保持相同的整备质量。宝马称,到2013年,“超大城市”的重量将进一步减轻。
“碳纤维时代”已现曙光
碳纤维优点较多,但高昂的成本影响普及。宝马如何控制“超大城市”的成本?据了解,“超大城市”使用的碳纤维由欧洲最大碳纤维制造商SGL集团提供,宝马与该集团建立了合资公司,在美国生产碳纤维。以前SGL主要致力于研发、生产航空航天用碳纤维,此次宝马与其合作研发出汽车用碳纤维。据了解,这种纤维的成本可降到车企能接受的水平。今后,宝马计划将这种材料销售给其他汽车企业和飞机、风电设备制造商。
为了进一步降低成本,宝马专门研发了一套程序,可以重新合成碳纤维碎料,实现废物利用。这意味着“超大城市”报废后,该车使用的碳纤维可以回收再利用,降低材料报废的损失,从而降低成本。
随着技术和工艺不断成熟,碳纤维有望成为汽车业的主流材料。虽然实现这个目标还有很长的路要走,但随着“超大城市”接近量产,人们似乎看到了汽车业“碳纤维时代”的曙光。这不是宝马自己的事,关乎整个汽车业的节能减排大业。
先行一步是实现反牵制的砝码
在批量生产的车型上大量使用碳纤维材料,宝马“超大城市”电动汽车开了先河。碳纤维的优点令汽车工程师难以抗拒,碳纤维车身能比钢质车身减轻50%的重量,比铝车身轻约30%。同时,碳纤维不存在腐蚀生锈的问题,比普通金属耐用。在极端气候条件下,碳纤维的性质几乎不发生变化,这是金属材料很难实现的。使用碳纤维制造车身,可以省去高成本、繁琐的涂装工艺。难怪有人说,碳纤维几乎是目前可知的最能让汽车减重的完美材料。
笔者似乎一直在简单地说碳纤维的好话,其实由此联想到了深层问题———中国汽车业长期为铁矿石价格波动所困的境遇。目前要求中国钢铁企业联合起来,打破力拓、必何必拓与淡水河谷三大矿业巨头对铁矿石的价格垄断显然不现实,中国汽车企业要想在材料上不受制于人,笔者认为最好的方法是自己积极推进新材料研发。因此,碳纤维对于中国汽车来说,具有重要的意义。虽然碳纤维看似离中国汽车很远,但任何科技成果在成功使用前,都要经历漫长的改进过程。要想在未来及时实现突破,必须完成技术积累。在碳纤维使用方面,宝马已经给我们上了一课,我们应有为跨国公司“上课”的准备和信心。
奔驰SL系列将使用碳纤维零部件
戴姆勒日前宣布,与日本东丽集团合作研发的碳纤维零部件计划配装在2012年推出的新款奔驰SL系列车型上,这些零部件将在东丽位于法国的工厂生产。今年4月,双方决定成立合资公司,共同研发汽车碳纤维零部件。
据了解,碳纤维复合材料成形技术是由东丽首创的,此次与戴姆勒合作,是该公司首次研发汽车碳纤维零部件。东丽是世界最大碳纤维制造企业,产品占全球碳纤维市场34%的份额。此前,东丽曾为法拉利提供车用碳纤维。
戴姆勒与东丽的合作成果,结合两家企业的先进技术,有望大幅缩短碳纤维复合材料的成形周期。两家企业的共同目标是,计划未来3年为戴姆勒的奔驰SL系列车型研发出新型复合材料零部件。戴姆勒计划通过与东丽合作,将奔驰系列车型白车身的重量降低10%,以此提高车辆的燃油效率,减少有害气体排放。
1992年,通用汽车展出超轻概念车(Ultralite Concept Car)。该车车身由碳纤维复合材料制成,采用手铺碳纤维预浸料工艺制造。该车车身质量为191公斤,由于用碳纤维取代钢材制造车身和底盘部件,该车整备质量减轻68%,节油约40%。
旧飞机或将提供再生碳纤维
如今汽车行业已成功使用大量再生材料,如废钢铁和铝,能用来铸造新的车身架构;旧水瓶能变成车用塑料部件等。如今,汽车能用的再生材料又多了一个来源———退役战斗机。此前,再生碳纤维不能立即为汽车所用,除非出现能提供足够可用废料的载体。如今,退役战斗机也许能扮演这个角色,因此能提高它们的再利用水平。
20世纪70年代,碳纤维首先应用在军用飞机上。20世纪80年代,碳纤维在飞机上得到普遍使用,当时知名战斗机F-18大黄蜂的机翼,便使用了大量碳纤维。旧飞机是再生碳纤维的良好供应体,其提供的再生碳纤维能够取代新生产的碳纤维。退役战斗机的机翼一般由强度高、重量轻的碳纤维制成,回收的机翼等部件切碎后,可用于制造汽车碳纤维零部件。
IAC集团北美生产与验证中心工程总监韦恩·沃勒说:“尽管飞机用碳纤维要在其他领域实现再利用仍有困难,但这个设想为降低车用碳纤维的成本提供了解决方案。”
目前再生碳纤维的价格水平不得而知。据了解,工业级碳纤维的成本约为每磅(约合0.45公斤)10美元;航天级碳纤维每磅约25美元。IAC正在进行再生碳纤维的测试工作,如果证明使用来自飞机的再生碳纤维可行,那么再生碳纤维的价格可能随产量提高而下降。
F-18大黄蜂战斗机的机翼使用大量碳纤维。
今年3月,日本帝人集团发布了PU_PA超轻电动概念车,采用帝人独有材料制成,包括碳纤维复合材料、聚碳酸酯树脂和生物衍生聚酯。该车整备质量仅为437公斤。