CAE技术在复杂SMC汽车零部件成型中的应用
By www.cfrp.com.cn
本文通过在复杂的SMC零件从制品设计到成型的过程中利用计算机模拟分析进行流动模拟、工艺设计等工作,从而阐明了该技术在复杂SMC零件生产过程中的有效性。
一、前言
汽车是现代交通运输的重要工具,其发展趋势为换型快,开发周期短,批量大、结构复杂。而复合材料具有重量轻、制造成本低、零部件集成度高等特点,在汽车制造中得到越来越广泛的应用。
复合材料与金属材料相比具有较大的优越性:
1、密度小,强度高。复合材料的密度一般在1.6~2.0g/cm3,约是钢的1/4,铝的2/3;其比强度与钢接近;2、热膨胀系数低。通过相关铺层设计,可使其热膨胀系数接近0,利用这一特点可制作尺寸精度要求高的构件;3、复合材料具有较好的减震性、隔热性、消音性、吸能性,可用于内、外饰、吸能器等零件,以减轻振动,减少噪音,保持车内温度,尤其是用作吸能器,具有优越的抗冲击性和弹性回复性,在车祸中可大大降低对人体的伤害;4、成本较低,可设计性强。
通过部件整合可以有效的降低汽车开发费用和生产成本,在中等批量的车型中采用复合材料取代铝材可降低成本40%,并且可缩短产品的开发周期。复合材料与钢铁相比具有明显的优势:具有关资料统计,可提高汽车质量23%,每辆汽车降低成本14%,重量减轻22%,零部件数量减少约22件,紧固件、附件数量减少27件。通过改变纤维、机体的种类及相对含量、纤维排列方式、铺层结构等可以满足复合材料结构与性能的各种要求,复合材料多为整体成型,如老式福特全顺汽车车头需要19个金属件和一个塑料件,而新式全顺汽车只需要一个SMC部件就可以实现,大大简化了工艺过程、减少加工时间、减少零件数量、减轻车身重量等。
相对于金属材料冲压成型来说,复合材料的模压成型是一个相对复杂、可预测性较差的过程,是在全封闭的环境中完成的。针对此特点其过程进行计算机模拟分析,使其过程和结果变为可以预测,从而明确其成型工艺方向,减少重复试验、缩短开发周期。
二、CAE技术在复杂SMC零件成型中的应用
计算机仿真技术是以多种科学理论为基础,以计算机及其相应的软件为工具,通过虚拟试验的方法分析和解决工程实际问题的一门综合技术,它具有经济、实用、灵活、可多次重复使用的优点,已经成为对许多复杂系统(工程的、非工程的)进行分析、设计、试验、评估必不可少的手段,也就是说,建立仿真模型并对其进行试验的一门技术。
SMC成型过程涉及到材料流变学、热传导学、反应动力学和液体力学等诸多交叉学科领域,是一个十分复杂的物理化学变化过程。这一过程可以抽象地分为三个方面:模压流动过程、纤维取向过程以及固化过程。对这三个过程做出准确、可靠的预测分析对SMC工艺的优化设计具有重要的意义。对复杂SMC零件而言,材料的流动对其成型起到决定性作用,合理的铺层设计将有助于材料在模腔的流动,而合理的流动对于产品成型和其结构功能的实现起到关键的作用。
通过引入计算机模拟这一过程将使材料的流动方向和流动时间可视化,从而指导铺层设计,确定前期对产品的工艺设计的方向,其基本的原理为:设SMC模压流动时为不可压缩的流体,结合动量、能量、质量守恒方程,得到SMC模压流动的控制方程。其控制方程包括压力分布方程、热传导方程和固化反应动力学方程等。对于薄壳件流动,如果假设模具表面没有滑移;流动中的主应力是剪应力。
由于SMC在模腔中流动过程是一个非线性的多场耦合问题,一方面模压料在模压过程中变形相当大;另一方面模压料的粘度随应变速率、温度和树脂固化度的可变性,使得其本构关系是非线性的。因此拟采用分步计算的方法,通过控制体有限元法来描述模压料的流动状况,而模压过程中的树脂流动问题是一个具有运动边界的非稳态过程。为了解决这一问题,我们将模压过程作为一系列准稳态的瞬间解的组合。在每一时间步,当压力场确定后,速度场可通过动量方程计算得到,新的流动前锋的位置可由流动前锋的速度分量和时间增量来估算。与压力场的求解相类似,温度场和转化率可根据当前的速度场来确定。由计算所得的温度和转化率则用于更新粘度,新的粘度值重新用于计算压力场,温度场和转化率计算,重复这一过程直至整个模腔充满,以汽车面罩产品为例:
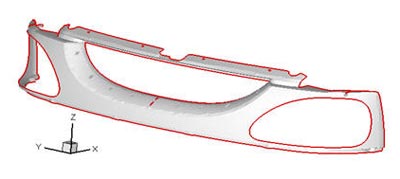
图1 面罩数模
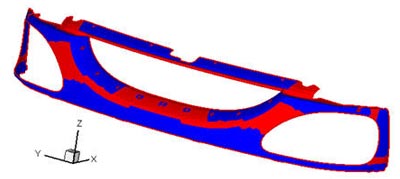
图2 铺料示意图
设定SMC模压流动过程中压力参数为1000MPa,温度参数为160℃,材料为4.2Kg,模腔厚度为3.5mm,其流动模拟图如下:
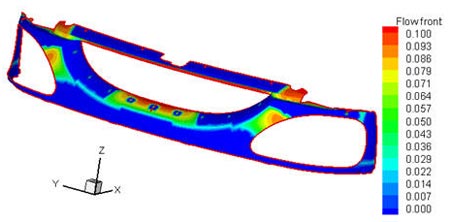
图3 模压料流动前沿模拟
观察材料的流动分析图不同颜色可以看到,材料流动所经历的时间不同,其中最长流动时间为0.1s,具体流动如下图:
.jpg)
图4 模压料流动区域划分
由上表可以看出,在所有成型条件正常时,产品表面状态不会出现较大问题,但若压力或者材料不稳定,在“3”、“4”区域较容易出现熔接痕和针孔等缺陷。而实际生产中所有条件不可能完全处于理想状态,“物、机、人”方面某个环节极有可能出现波动,为了确保产品品质的稳定性,我们参照计算机模拟结果,对铺料方式进行了适当改进,做出了如下的铺料图,在产品试模时取得了较圆满的结果,节省产品试模时间。
.jpg)
图5 产品实际辅料图
三、结束语
计算机模拟分析已经广泛的应用到各个领域中去了,在玻璃钢行业目前模拟分析主要用在零件的结构分析,产品的成型模拟分析等方面,随着模拟分析的推广,目前出现了较大的分析软件,如ANSYS、ALGOR、ASAQUS、NASRRAN等,虽然每种软件操作不同,侧重点也有所差异,但其目的都是一样的,就是希望通过模拟,使过程和结果可视化,从而避免失误,减少开发费用,缩短开发周期
本文通过在复杂的SMC零件从制品设计到成型的过程中利用计算机模拟分析进行流动模拟、工艺设计等工作,从而阐明了该技术在复杂SMC零件生产过程中的有效性。
一、前言
汽车是现代交通运输的重要工具,其发展趋势为换型快,开发周期短,批量大、结构复杂。而复合材料具有重量轻、制造成本低、零部件集成度高等特点,在汽车制造中得到越来越广泛的应用。
复合材料与金属材料相比具有较大的优越性:
1、密度小,强度高。复合材料的密度一般在1.6~2.0g/cm3,约是钢的1/4,铝的2/3;其比强度与钢接近;2、热膨胀系数低。通过相关铺层设计,可使其热膨胀系数接近0,利用这一特点可制作尺寸精度要求高的构件;3、复合材料具有较好的减震性、隔热性、消音性、吸能性,可用于内、外饰、吸能器等零件,以减轻振动,减少噪音,保持车内温度,尤其是用作吸能器,具有优越的抗冲击性和弹性回复性,在车祸中可大大降低对人体的伤害;4、成本较低,可设计性强。
通过部件整合可以有效的降低汽车开发费用和生产成本,在中等批量的车型中采用复合材料取代铝材可降低成本40%,并且可缩短产品的开发周期。复合材料与钢铁相比具有明显的优势:具有关资料统计,可提高汽车质量23%,每辆汽车降低成本14%,重量减轻22%,零部件数量减少约22件,紧固件、附件数量减少27件。通过改变纤维、机体的种类及相对含量、纤维排列方式、铺层结构等可以满足复合材料结构与性能的各种要求,复合材料多为整体成型,如老式福特全顺汽车车头需要19个金属件和一个塑料件,而新式全顺汽车只需要一个SMC部件就可以实现,大大简化了工艺过程、减少加工时间、减少零件数量、减轻车身重量等。
相对于金属材料冲压成型来说,复合材料的模压成型是一个相对复杂、可预测性较差的过程,是在全封闭的环境中完成的。针对此特点其过程进行计算机模拟分析,使其过程和结果变为可以预测,从而明确其成型工艺方向,减少重复试验、缩短开发周期。
二、CAE技术在复杂SMC零件成型中的应用
计算机仿真技术是以多种科学理论为基础,以计算机及其相应的软件为工具,通过虚拟试验的方法分析和解决工程实际问题的一门综合技术,它具有经济、实用、灵活、可多次重复使用的优点,已经成为对许多复杂系统(工程的、非工程的)进行分析、设计、试验、评估必不可少的手段,也就是说,建立仿真模型并对其进行试验的一门技术。
SMC成型过程涉及到材料流变学、热传导学、反应动力学和液体力学等诸多交叉学科领域,是一个十分复杂的物理化学变化过程。这一过程可以抽象地分为三个方面:模压流动过程、纤维取向过程以及固化过程。对这三个过程做出准确、可靠的预测分析对SMC工艺的优化设计具有重要的意义。对复杂SMC零件而言,材料的流动对其成型起到决定性作用,合理的铺层设计将有助于材料在模腔的流动,而合理的流动对于产品成型和其结构功能的实现起到关键的作用。
通过引入计算机模拟这一过程将使材料的流动方向和流动时间可视化,从而指导铺层设计,确定前期对产品的工艺设计的方向,其基本的原理为:设SMC模压流动时为不可压缩的流体,结合动量、能量、质量守恒方程,得到SMC模压流动的控制方程。其控制方程包括压力分布方程、热传导方程和固化反应动力学方程等。对于薄壳件流动,如果假设模具表面没有滑移;流动中的主应力是剪应力。
由于SMC在模腔中流动过程是一个非线性的多场耦合问题,一方面模压料在模压过程中变形相当大;另一方面模压料的粘度随应变速率、温度和树脂固化度的可变性,使得其本构关系是非线性的。因此拟采用分步计算的方法,通过控制体有限元法来描述模压料的流动状况,而模压过程中的树脂流动问题是一个具有运动边界的非稳态过程。为了解决这一问题,我们将模压过程作为一系列准稳态的瞬间解的组合。在每一时间步,当压力场确定后,速度场可通过动量方程计算得到,新的流动前锋的位置可由流动前锋的速度分量和时间增量来估算。与压力场的求解相类似,温度场和转化率可根据当前的速度场来确定。由计算所得的温度和转化率则用于更新粘度,新的粘度值重新用于计算压力场,温度场和转化率计算,重复这一过程直至整个模腔充满,以汽车面罩产品为例:
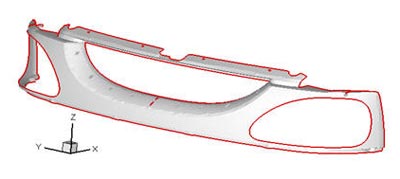
图1 面罩数模
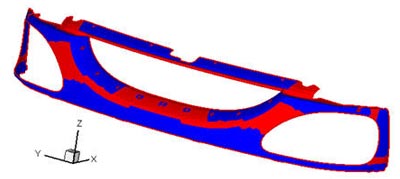
图2 铺料示意图
设定SMC模压流动过程中压力参数为1000MPa,温度参数为160℃,材料为4.2Kg,模腔厚度为3.5mm,其流动模拟图如下:
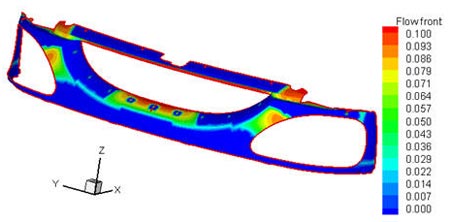
图3 模压料流动前沿模拟
观察材料的流动分析图不同颜色可以看到,材料流动所经历的时间不同,其中最长流动时间为0.1s,具体流动如下图:
.jpg)
图4 模压料流动区域划分
.jpg)
由上表可以看出,在所有成型条件正常时,产品表面状态不会出现较大问题,但若压力或者材料不稳定,在“3”、“4”区域较容易出现熔接痕和针孔等缺陷。而实际生产中所有条件不可能完全处于理想状态,“物、机、人”方面某个环节极有可能出现波动,为了确保产品品质的稳定性,我们参照计算机模拟结果,对铺料方式进行了适当改进,做出了如下的铺料图,在产品试模时取得了较圆满的结果,节省产品试模时间。
.jpg)
图5 产品实际辅料图
三、结束语
计算机模拟分析已经广泛的应用到各个领域中去了,在玻璃钢行业目前模拟分析主要用在零件的结构分析,产品的成型模拟分析等方面,随着模拟分析的推广,目前出现了较大的分析软件,如ANSYS、ALGOR、ASAQUS、NASRRAN等,虽然每种软件操作不同,侧重点也有所差异,但其目的都是一样的,就是希望通过模拟,使过程和结果可视化,从而避免失误,减少开发费用,缩短开发周期