CFRP加工切削面表面粗糙度仅Ra0.4μm,既无分层也无残留
By www.carbonfiber.com.cn
碳纤维增强树脂基复合材料(CFRP)是在碳纤维上层叠多层浸渍了环氧树脂的片材(预浸材),然后加热加压制成的。因此在切削时容易出现的问题是预浸材之间和纤维之间出现分层和劈裂。解决了这些问题,开始面向摩托车和汽车策划、设计和生产CFRP部件的是日本东京R&D公司(总部:东京)(图1)。

图1:日本东京R&D的加工实例和使用的机床
主要面向摩托车和赛车加工CFRP部件,从部件的提案到设计、成形、加工提供一条龙服务。左图为发动机上的导流部件——通风筒的加工实例。CFRP切削使用的加工中心是山崎马扎克的“VTC-200B”(右图)和发那科的“ROBODRILL α-T14iAL”。
过去只有一级方程式赛车(F1)及MotoGP等赛车的零部件对CFRP存在需求。每种赛车零部件需要的个数都很少。因此,与其用昂贵的夹具机械切削,不如用旋转工具人工切削成本更低。东京R&D从15年前就开始积累机械切削CFRP的技术经验,但此前都不大有用武之地。
东京R&D制造部部长白岩一行表示“但最近1~2年,形势大大改变”。因为不仅是赛车,量产型汽车也开始采用CFRP。
重要的“工具材质”
东京R&D的优势在于切削面的品质高。图2是该公司制造的回纹针样品。大小跟500日元硬币差不多,仔细观察发现厚度方向上有三层。整体厚度为900μm,每层相差300μm。这么微细的加工也没出现分层和残留,表面粗糙度仅Ra1.6μm。另外,该公司的其他部件有的表面粗糙度仅Ra0.4μm。

图2:通过微细加工也能实现平滑的切削面
这是制造的回纹针样品。厚度为900μm,设有300μm的高度差。这么微细的加工也很光滑,表面粗糙度仅Ra1.6μm。加工时间为3分钟。
据东京R&D介绍,切削CFRP主要有三大技巧。即[1]根据切削部位区别使用工具,[2]根据部位调整工具的旋转方向和转速以及进刀方向和速度,[3]合理设定切削程序。下面逐条来介绍。
首先是[1]区别使用工具,了解什么样的工具适合什么样的切削至关重要。
比如,切削CFRP主要使用超硬合金工具,而超硬合金工具也分有金刚石涂层的和无金刚石涂层的。据该公司制造部机械加工组组长国益彻也介绍,要想实现平滑的切削面,关键在于工具的“锋锐度”。国益介绍说:“无金刚石涂层的工具在锋锐度方面更为出色,但缺点是磨损得快。关键是如何使用短寿命工具实现平滑的切削面”。
顺便一提,东京R&D还在工具厂商的帮助下开发出了将金刚石砂粒电沉积在机械构造用碳钢(S45C)上的自制工具(图3)。
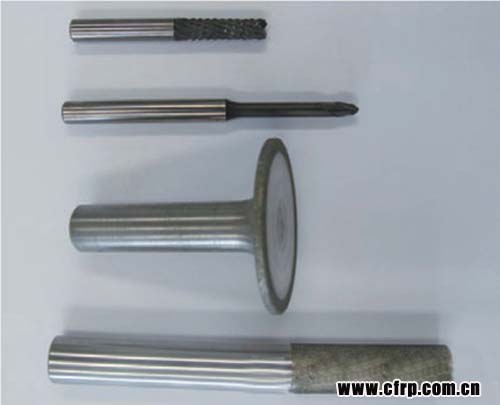
图3:CFRP加工中使用的部分工具
上面的两个是通过CVD(化学气相沉淀)涂布了金刚石的超硬合金立铣刀,属于市售工具。下面两个是电沉积了金刚石砂粒的工具,是在工具厂商协助下自制的工具。
2]工具的旋转和进刀方面,加工CFRP特别需要注意的是工具的旋转方向和进刀方向。因为由预浸材层叠而成的CFRP具有各向异性。
图4表示切削采用了UD预浸材(仅一个方向配备了碳纤维)的CFRP时的工具旋转方向和进刀方向。工具的刀刃顺时针方向旋转时,在刀刃远离工件的部分,刀刃沿着上挑纤维的方向移动。因此,这一部分容易出现分层。于是,从右向左进刀,刀刃对着工件始终在压着纤维的方向上移动。这样,就可以防止分层。
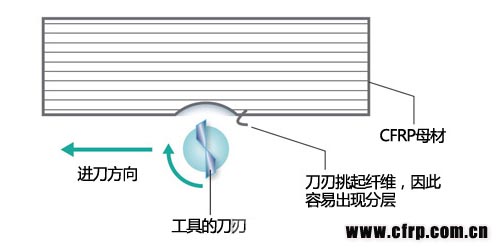
图4:加工UD(单方向)预浸材的CFRP时的刀具旋转方向和进刀方向
图为俯视工件和工具的状态。在CFRP切削中,工具的旋转方向与进刀方向的关系非常主要。之所以容易分层,是因为在刀刃远离工件的部分,刀刃沿着从工件上上挑纤维的方向移动。这时,如果从右向左进刀,刀刃就会沿着始终压着纤维的方向移动,能够避免分层。
虽然道理很简单,但要不断积累这么精细的技巧才能实现平滑的切削面。不过,该公司未公布具体的工具转数和进刀速度。
下料量也有讲究
3]切削程序方面,也需要下细工夫。为了浅显易懂地说明重点,笔者将比较由芳轮纤维与碳纤维交织的片材层叠而成的复合材料的切削程序与普通CFRP的切削程序。
以两种材料都开直径10mm的孔为例。普通CFRP在粗加工时首先从直径10mm中切掉中心直径9.8mm。然后,用合适的工具精加工剩下的下料(厚度为100μm的中空圆筒)。
而上述的复合材料在粗加工时切掉比CFRP小的直径,保留更多下料。并且,通过精加工,一下去掉剩余的厚度。因为这样的话,芳轮纤维“发粘,容易出现残留”(国益)。这样的材料最好多留下料,一下切掉。
这里比较了复合材料和CFRP,但CFRP也有很多种,因此可以采用同一方法。除材料特性外,根据板厚和加工形状分配粗加工和精加工也非常重要。
东京R&D计划利用这些经验,打入量产摩托车和汽车零部件市场,同时扩大飞机领域的业务。
碳纤维增强树脂基复合材料(CFRP)是在碳纤维上层叠多层浸渍了环氧树脂的片材(预浸材),然后加热加压制成的。因此在切削时容易出现的问题是预浸材之间和纤维之间出现分层和劈裂。解决了这些问题,开始面向摩托车和汽车策划、设计和生产CFRP部件的是日本东京R&D公司(总部:东京)(图1)。

图1:日本东京R&D的加工实例和使用的机床
主要面向摩托车和赛车加工CFRP部件,从部件的提案到设计、成形、加工提供一条龙服务。左图为发动机上的导流部件——通风筒的加工实例。CFRP切削使用的加工中心是山崎马扎克的“VTC-200B”(右图)和发那科的“ROBODRILL α-T14iAL”。
过去只有一级方程式赛车(F1)及MotoGP等赛车的零部件对CFRP存在需求。每种赛车零部件需要的个数都很少。因此,与其用昂贵的夹具机械切削,不如用旋转工具人工切削成本更低。东京R&D从15年前就开始积累机械切削CFRP的技术经验,但此前都不大有用武之地。
东京R&D制造部部长白岩一行表示“但最近1~2年,形势大大改变”。因为不仅是赛车,量产型汽车也开始采用CFRP。
重要的“工具材质”
东京R&D的优势在于切削面的品质高。图2是该公司制造的回纹针样品。大小跟500日元硬币差不多,仔细观察发现厚度方向上有三层。整体厚度为900μm,每层相差300μm。这么微细的加工也没出现分层和残留,表面粗糙度仅Ra1.6μm。另外,该公司的其他部件有的表面粗糙度仅Ra0.4μm。

图2:通过微细加工也能实现平滑的切削面
这是制造的回纹针样品。厚度为900μm,设有300μm的高度差。这么微细的加工也很光滑,表面粗糙度仅Ra1.6μm。加工时间为3分钟。
据东京R&D介绍,切削CFRP主要有三大技巧。即[1]根据切削部位区别使用工具,[2]根据部位调整工具的旋转方向和转速以及进刀方向和速度,[3]合理设定切削程序。下面逐条来介绍。
首先是[1]区别使用工具,了解什么样的工具适合什么样的切削至关重要。
比如,切削CFRP主要使用超硬合金工具,而超硬合金工具也分有金刚石涂层的和无金刚石涂层的。据该公司制造部机械加工组组长国益彻也介绍,要想实现平滑的切削面,关键在于工具的“锋锐度”。国益介绍说:“无金刚石涂层的工具在锋锐度方面更为出色,但缺点是磨损得快。关键是如何使用短寿命工具实现平滑的切削面”。
顺便一提,东京R&D还在工具厂商的帮助下开发出了将金刚石砂粒电沉积在机械构造用碳钢(S45C)上的自制工具(图3)。
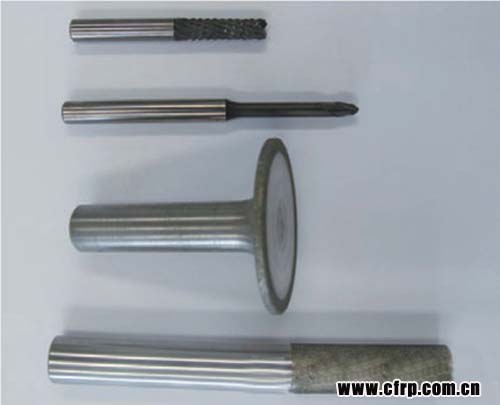
图3:CFRP加工中使用的部分工具
上面的两个是通过CVD(化学气相沉淀)涂布了金刚石的超硬合金立铣刀,属于市售工具。下面两个是电沉积了金刚石砂粒的工具,是在工具厂商协助下自制的工具。
2]工具的旋转和进刀方面,加工CFRP特别需要注意的是工具的旋转方向和进刀方向。因为由预浸材层叠而成的CFRP具有各向异性。
图4表示切削采用了UD预浸材(仅一个方向配备了碳纤维)的CFRP时的工具旋转方向和进刀方向。工具的刀刃顺时针方向旋转时,在刀刃远离工件的部分,刀刃沿着上挑纤维的方向移动。因此,这一部分容易出现分层。于是,从右向左进刀,刀刃对着工件始终在压着纤维的方向上移动。这样,就可以防止分层。
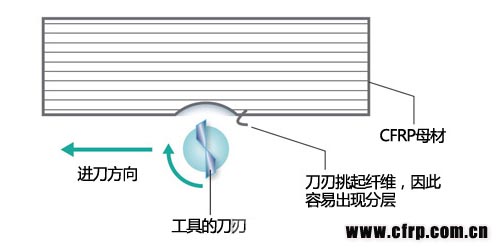
图4:加工UD(单方向)预浸材的CFRP时的刀具旋转方向和进刀方向
图为俯视工件和工具的状态。在CFRP切削中,工具的旋转方向与进刀方向的关系非常主要。之所以容易分层,是因为在刀刃远离工件的部分,刀刃沿着从工件上上挑纤维的方向移动。这时,如果从右向左进刀,刀刃就会沿着始终压着纤维的方向移动,能够避免分层。
虽然道理很简单,但要不断积累这么精细的技巧才能实现平滑的切削面。不过,该公司未公布具体的工具转数和进刀速度。
下料量也有讲究
3]切削程序方面,也需要下细工夫。为了浅显易懂地说明重点,笔者将比较由芳轮纤维与碳纤维交织的片材层叠而成的复合材料的切削程序与普通CFRP的切削程序。
以两种材料都开直径10mm的孔为例。普通CFRP在粗加工时首先从直径10mm中切掉中心直径9.8mm。然后,用合适的工具精加工剩下的下料(厚度为100μm的中空圆筒)。
而上述的复合材料在粗加工时切掉比CFRP小的直径,保留更多下料。并且,通过精加工,一下去掉剩余的厚度。因为这样的话,芳轮纤维“发粘,容易出现残留”(国益)。这样的材料最好多留下料,一下切掉。
这里比较了复合材料和CFRP,但CFRP也有很多种,因此可以采用同一方法。除材料特性外,根据板厚和加工形状分配粗加工和精加工也非常重要。
东京R&D计划利用这些经验,打入量产摩托车和汽车零部件市场,同时扩大飞机领域的业务。