A350的复合材料构件制造
By www.carbonfiber.com.cn
A350是迄今为止被认为复合材料用量占全机结构重量比例最大的一种客机,其复合材料结构重量占全机结构重量52%,超过了波音787复合材料结构重量比例的50%。由于复合材料构件都比较大,质量要求更加严格,在设备上、工艺流程上也带来了许多新的要求,本文即对该飞机的复合材料大型构件的制造进行阐述。
机身的复合材料构件制造
A350的机身如图1所示,机头段(11~12段)和机身前段(13~14段),联接后称为前机身;15段为机身中段,又称中机身;16~18段为含压力框的整段,合称机身后段,其与桶形后罩(19段)联接后称为后机身。机身直径为5.89m,在A350-900上,3段分别长13m (13~14段)、20m(15段)和15m(16~18段)。其中,机身中段(15段)如图2所示。
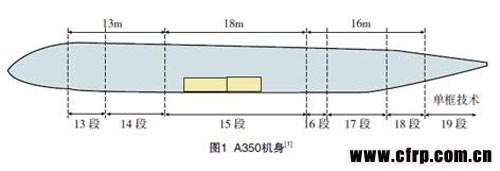
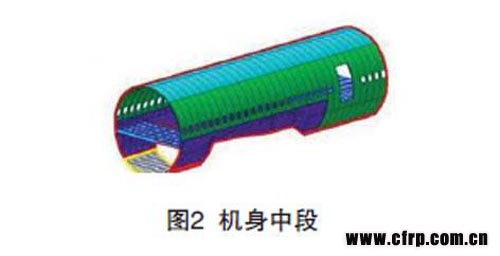
2 中机身[2]
中机身,由6个复合材料板件、地板和隔框等构件构成。该板件由Spirit AeroSystems 制造
ElectroImpact公司为Spirit公司设计制造了专用于A350机身板件铺放的双头自动纤维铺放机,该机不但可完成铺放,而且可执行切割动作,能够完全双向铺倾斜且复杂的表面,进给速度达50.8m/min。大型机身壁板铺丝速度要求高,该机床通过新的设计实现了切割,优化进给、丝束路径等的需要。
机床在殷纳钢阳模上铺Hexply M-21E碳纤维/ Hexcel增韧环氧预浸料。所有的15段壁板包含有整体的CFRP桁条,该桁条是采用悬臂类AFP机床制造的二维夹层件(采用MTorres桁条铺设设备铺设)。桁条铺设后放在复合材料壁板槽内,在热压罐(长为24.4m、宽为6.7m)中进行共固化。
MTorres公司还为Spirit公司提供2台高5m、长15m的Torresonic UT柱形超声检测设备,该设备上装有Kuka Roboter GMBH(Ausburg德国)的机器人装置,可同时检测机身壁板的内外蒙皮。检测完成后,装上防雷击的外部铜网,与ESN(电结构网络)连结,然后将复合材料壁板连接到机身框上。
大部分机身框为铝合金制造(1000型部分隔框正考虑用新工艺BRaF编织结构制造复合材料隔框)。此外,舱门椽为钛合金,框和椽使用自动设备连接。
2 前机身[2]
13~14段由4个复合材料板件加上地板构件、隔框等构成(图3)。该复合材料板件由德国Nordenham的premium Aerotec空客公司生产。这4个13m长复合材料板件,其所用材料,技术标准、工艺方法与15段相同,只是尺寸不同。最大的是前机身右侧板件,面积为93m2。4个板件和地板构件组合后进行超声、修正、钻孔,完成机加工序后运到Saint-Nazaire工厂,与在法国Aerolie制造并运到此处的机头部件(11~12段)对合成为前机身,图4为机头部分(11~12段)。


该机头在法国的空客Aerolia工厂制造,Aerolia为制造该机头,建立了5个制造区:1个530m2的铺层清洁间;一个7m×14m的热压罐;一条表面处理生产线;超声检验区;装配区。
11段是铝结构,12段是复合材料结构,其铺设见图5。

3 后机身[2-3]
机身16~18段在德国的Ausburg生产,也是4个复合材料板件组合,工艺流程基本和中机身一样。汉堡是空客A380主要部件的生产区,有强大的复合材料构件制造能力。在汉堡完成系统件安装后也运到法国到图卢兹总装厂。
19段在西班牙的Illescas生产。 后机身段(16~18段)与后机身桶子段(19段)对接成后机身。后机身桶子段和波音787机身生产方法类似,在纤维铺放机上铺设。
后机身的压力框和地板构件均在德国的空客Aerotec工厂生产。压力框用CFRP制造,其工艺方法VAP(Vacuum Assisted Process)是一种抽真空渗渍工艺。这是该公司发展并取得专利的一项专用于制造压力框的技术,已在A380、A400M和波音787中使用。其特点是将纤维布剪裁缝合或纤维丝编织成产品形状,铺放在工装上进行密封,将外部的树脂熔化,真空抽入,开发了一种专用的微孔薄膜,隔离空气,可进热压罐也可不进热压罐,是制造出的产品孔隙率低,纤维含量高的一种工艺方法。这也属于热压罐外固化(Out of Autoclave,OOA)工艺的一种。
机身龙骨梁虽然主要受力件用了钛合金结构,但该梁尺寸为16.6m×4.0m,重为1180kg,复合材料件仍占70%。
机翼的复合材料构件制造[2-4]
1 前翼梁制造
A350的前翼梁是长为31.2m的结构件,是Spirit公司制造的最大的梁,也是Spirit公司制造的第一个全复合材料梁,该梁从翼根到翼尖由3部件组成,即长为7m的内侧梁、长为12.7m的中梁和长为11.5m的外侧梁。梁的制造是采用100层碳纤维增强塑料,从内侧梁根部的宽1.8m处逐渐过渡到外侧梁翼尖的宽0.3m处。
M Torres公司是Spirit开发梁生产能力的关键合作伙伴。公司的自动纤维铺放系统相比于普通台架式或柱式机床具有更大柔性和生产率。据报道,这些AFP系统铺设速度高达60m/min,远高于以前的速度,使梁生产工艺经济可行。M Torres公司已经向GKN航宇公司交付一台类似设备,用于生产A350后翼梁。这些机床是为实现沿着梁的边缘严格的U形几何形状而开发的,因为在按45°角铺设到90°弯角时,梁的边缘容易产生许多问题。机床头还可以承受高温和更大压力,适用于低粘度Hexply材料,即用于铺叠与机身壁板的同样M21-E增韧环氧预浸料。每台M Torres机床可以同时在殷钢芯轴上铺2个长为15m的梁,然后转移到热压罐中进行固化。
固化梁要使用自动台架TORRESONIC UT检测仪进行质量检查,该检测仪的检测范围长为15m,宽为2 m。MTorres公司制造框架和装上通用机器人,机器人由德国Kuka Roboter GMBH (Ausburg 德国)公司提供,电子设备由Techaton (Madrid 西班牙)供应。完成的梁部件运到Spirit公司位于苏格兰的Prestwick工厂,3段连接到一起,并与固定前缘和其他定位装置对接,然后交付完整的前缘组件给空客的Broughton工厂进行机翼总装。
2 后翼梁制造
后翼梁在GKN(Reddich Worchester英国)生产,MTorres公司提供了类似设备。由于该梁要和固定后缘对接,并要承当来自动翼的力,该公司除了制造梁以外,还负责将GE公司制造的固定机翼后缘(FTE)固定到后梁上。并进行最后检验,合格后重新将固定后缘分解,以便运输。
后梁包括3段,每段长为10m,最重要的是内侧的那段梁,重约500kg,其根部层压达25~30mm厚,中段梁重为150kg,最外的一段重为100kg。
每段梁都用纤维铺放机铺设,用殷纳钢模具。桶形的,固化后切成2个C形梁。材料是Hexcel的碳纤维环氧预浸料M-21E。带宽为0.64cm。前面已经提到所用铺放机也是M.Torres提供的,五坐标自动控制,模具固定在转动心轴上铺设。机器可按要求自动控制铺放厚度。铺设完后的热压罐固化和检验同前梁一样。
3 机翼上板件制造
机翼上部蒙皮在空客德国汉堡总部所属的空客Stade工厂生产,此处工房面积为30000m2,不但可铺碳纤维带,还第一次开发了玻璃纤维的铺设,该机翼板件31.6m×5.6m,所用热压罐是当前世界上技术最先进直径最大者之一,能同时固化2个板件。该热压罐据说直径是8m,而空客在制造A380时所用热压罐直径为6m。
除铺制机翼板件蒙皮外,该厂还生产用于该板件的长桁,为此该厂建了一条140m的生产线。在质量控制方面,引进了适用于该板件CFRP内外表面同时检查的的检查系统。对边缘的修整用水切割。在工房里建立了自动运输系统。
该全套设施也用于A350垂尾的制造。
4 机翼下板件制造
机翼下板件在西班牙Illescas 生产,所用技术条件、标准、工艺流程、设备与上板件一致。
上下机翼板件完工后均运至Broughton(英国)进行机翼装配。 Illescas还同时生产A350机身19段。
5 机翼固定后缘制造
机翼固定后缘由GE公司生产。后缘是蜂窝结构,原用Hexply8552预浸料胶接蒙皮和Hexcel蜂窝芯子Hexweb HRH-36,该芯子由Hexcel下料机加后交到GE公司。现在UMECO公司根据GE的要求开发了OOA的MTM-44-1预浸料,该新材料的特点是密度低,预制品密封袋装好后,抽真空并加温,130℃时开始固化,180℃时固化完成。挥发气少、孔隙率低。由于不需加压,可以不进热压罐,节约造价。
6 机翼前缘制造
机翼前缘在英国苏格兰 Spirit Aerosystems Europe的普雷斯蒂克工厂设计制造,部份零组件安排在其在马来西亚Subang工厂生产(如下板件)。该前缘长接近32m,其中50%是碳纤维构件。
7 中央翼制造
中央翼由EADS在Nante(法国南特)的工厂生产,40%的碳纤维(CFRP)件。翼盒长为6.5m,高为3.9m,表面面积为36m2,其板件是Nante生产过的最大复合材料件。技术标准、工艺流程、工艺方法基本和机翼部分一致。中央翼完工后运至法国St Nazaire,在那里和机身对接。
8 襟副翼制造
襟副翼也主要是复合材料结构。GKN公司承担为A350制造襟翼,该合同在德国幕尼黑签订。GKN又将承包的外襟翼转包给荷兰Stork Fokker公司生产,Fokker公司在Papendrecht制造外襟翼。内襟翼即由GKN在Bremen生产。
尾翼制造
空客德国Stade分部承担了A350尾翼的设计工作,并承担垂直尾翼的制造。尾翼整个是以碳纤维(CFRP)为主。Stade拥有强大的复合材料构件制造能力,除承当A350机翼上板件生产外还有足够的实力(包括设备)来完成垂尾制造计划。 西班牙的 Puero Real于2011年开始制造A350的水平尾翼,该处拥有强大的自动钻孔设备和铺放能力以及无损检测能力。
尾翼的方向舵,升降舵即通过西班牙安排在哈尔滨哈飞与空客合资的企业生产。该合资公司配备了铺带机及有关的检验设备。
结束语
A350的制造分工比较杂,其第一供应商参与总体设计并承包分工部件的整个部件设计,除自己承当部分制造任务外还将部分制造工作外扩到第二承包商,甚至还有第三承包商,但第二承包商以下都不再有设计权限。
总的情况是前机身在德国总成,中机身在美国总成,后机身也在德国总成,机翼在英国总成,尾翼在西班牙总成,中央翼在法国总成,这些总成单位就是当然的第一承包单位。最后都交到法国图鲁兹进行总装配。
总之,复合材料在飞机上的应用正日益增大,A350中52%的占有量虽是空前,但决非绝后。A350在铺带铺丝工艺上比A380又有许多突破。从当前复合材料构件制造来看,全工艺过程必须紧紧抓住铺放(铺带或铺丝)、机加铣切、钻孔、无损超声几个主要环节,缝合技术在机身后压力框等部件中已开始采用。随着A350-1000型的开发还正在研究一些更新的技术使用。
值得一提的是,空客还在考虑继续扩大复合材料使用范围,例如将发展的1000型,总长将比900型长7m,要增加 11个隔框。要减少由于增加隔框而相应增加过多重量,他们准备用BRaF (Braided Frame)即隔框编织法来制造这些复合材料隔框。其过程就是将干纤维带通过编织预成型件和机身直径相同的预成型件,然后注树脂,固化后修正成为框的成品,而不再通过预浸带来铺设。此外还在研究用FPP(Fiber Patch Perform),是一种干脆用纤维丝束小片的预成型法,它通过机械手来安放微小的补片,注入树脂制造零件,并用于零件(如窗口边缘)的局部加强,下一步计划是准备用于制造复合材料长桁的预成型件,使重量更轻、成本更低。而有关这些新技术所需新设备的充实和现代化又是个重要问题。
参考文献:
[1] 范玉青,张丽华.超大型复合材料机体部件应用技术的新进展.航空学报,2009,30(3):534-543.
[2] George M. Automating aerospace composites production with fiber placement. Reinforced Plastic,2011,55(3):31-37.
[3] Leeuwen M V.First A350XWB aft fuselage built[EB/OL]. 2012[2013-5-12].http://www.aviationnews.eu/2012/03/14/ first-a350-xwb-aft-fuselage-built/
[4] Gardiner G.A350 XWB Update: Smart manufacturing[EB/OL].2011[2013-5-16].http://www.compositesworld.com/articles/a350-xwb-update-smart-manufacturing.
A350是迄今为止被认为复合材料用量占全机结构重量比例最大的一种客机,其复合材料结构重量占全机结构重量52%,超过了波音787复合材料结构重量比例的50%。由于复合材料构件都比较大,质量要求更加严格,在设备上、工艺流程上也带来了许多新的要求,本文即对该飞机的复合材料大型构件的制造进行阐述。
机身的复合材料构件制造
A350的机身如图1所示,机头段(11~12段)和机身前段(13~14段),联接后称为前机身;15段为机身中段,又称中机身;16~18段为含压力框的整段,合称机身后段,其与桶形后罩(19段)联接后称为后机身。机身直径为5.89m,在A350-900上,3段分别长13m (13~14段)、20m(15段)和15m(16~18段)。其中,机身中段(15段)如图2所示。
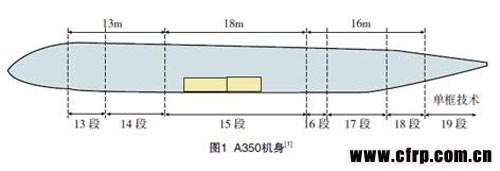
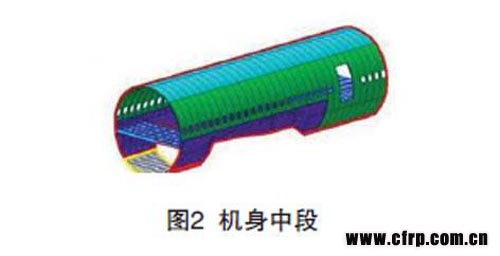
2 中机身[2]
中机身,由6个复合材料板件、地板和隔框等构件构成。该板件由Spirit AeroSystems 制造
ElectroImpact公司为Spirit公司设计制造了专用于A350机身板件铺放的双头自动纤维铺放机,该机不但可完成铺放,而且可执行切割动作,能够完全双向铺倾斜且复杂的表面,进给速度达50.8m/min。大型机身壁板铺丝速度要求高,该机床通过新的设计实现了切割,优化进给、丝束路径等的需要。
机床在殷纳钢阳模上铺Hexply M-21E碳纤维/ Hexcel增韧环氧预浸料。所有的15段壁板包含有整体的CFRP桁条,该桁条是采用悬臂类AFP机床制造的二维夹层件(采用MTorres桁条铺设设备铺设)。桁条铺设后放在复合材料壁板槽内,在热压罐(长为24.4m、宽为6.7m)中进行共固化。
MTorres公司还为Spirit公司提供2台高5m、长15m的Torresonic UT柱形超声检测设备,该设备上装有Kuka Roboter GMBH(Ausburg德国)的机器人装置,可同时检测机身壁板的内外蒙皮。检测完成后,装上防雷击的外部铜网,与ESN(电结构网络)连结,然后将复合材料壁板连接到机身框上。
大部分机身框为铝合金制造(1000型部分隔框正考虑用新工艺BRaF编织结构制造复合材料隔框)。此外,舱门椽为钛合金,框和椽使用自动设备连接。
2 前机身[2]
13~14段由4个复合材料板件加上地板构件、隔框等构成(图3)。该复合材料板件由德国Nordenham的premium Aerotec空客公司生产。这4个13m长复合材料板件,其所用材料,技术标准、工艺方法与15段相同,只是尺寸不同。最大的是前机身右侧板件,面积为93m2。4个板件和地板构件组合后进行超声、修正、钻孔,完成机加工序后运到Saint-Nazaire工厂,与在法国Aerolie制造并运到此处的机头部件(11~12段)对合成为前机身,图4为机头部分(11~12段)。


该机头在法国的空客Aerolia工厂制造,Aerolia为制造该机头,建立了5个制造区:1个530m2的铺层清洁间;一个7m×14m的热压罐;一条表面处理生产线;超声检验区;装配区。
11段是铝结构,12段是复合材料结构,其铺设见图5。

3 后机身[2-3]
机身16~18段在德国的Ausburg生产,也是4个复合材料板件组合,工艺流程基本和中机身一样。汉堡是空客A380主要部件的生产区,有强大的复合材料构件制造能力。在汉堡完成系统件安装后也运到法国到图卢兹总装厂。
19段在西班牙的Illescas生产。 后机身段(16~18段)与后机身桶子段(19段)对接成后机身。后机身桶子段和波音787机身生产方法类似,在纤维铺放机上铺设。
后机身的压力框和地板构件均在德国的空客Aerotec工厂生产。压力框用CFRP制造,其工艺方法VAP(Vacuum Assisted Process)是一种抽真空渗渍工艺。这是该公司发展并取得专利的一项专用于制造压力框的技术,已在A380、A400M和波音787中使用。其特点是将纤维布剪裁缝合或纤维丝编织成产品形状,铺放在工装上进行密封,将外部的树脂熔化,真空抽入,开发了一种专用的微孔薄膜,隔离空气,可进热压罐也可不进热压罐,是制造出的产品孔隙率低,纤维含量高的一种工艺方法。这也属于热压罐外固化(Out of Autoclave,OOA)工艺的一种。
机身龙骨梁虽然主要受力件用了钛合金结构,但该梁尺寸为16.6m×4.0m,重为1180kg,复合材料件仍占70%。
机翼的复合材料构件制造[2-4]
1 前翼梁制造
A350的前翼梁是长为31.2m的结构件,是Spirit公司制造的最大的梁,也是Spirit公司制造的第一个全复合材料梁,该梁从翼根到翼尖由3部件组成,即长为7m的内侧梁、长为12.7m的中梁和长为11.5m的外侧梁。梁的制造是采用100层碳纤维增强塑料,从内侧梁根部的宽1.8m处逐渐过渡到外侧梁翼尖的宽0.3m处。
M Torres公司是Spirit开发梁生产能力的关键合作伙伴。公司的自动纤维铺放系统相比于普通台架式或柱式机床具有更大柔性和生产率。据报道,这些AFP系统铺设速度高达60m/min,远高于以前的速度,使梁生产工艺经济可行。M Torres公司已经向GKN航宇公司交付一台类似设备,用于生产A350后翼梁。这些机床是为实现沿着梁的边缘严格的U形几何形状而开发的,因为在按45°角铺设到90°弯角时,梁的边缘容易产生许多问题。机床头还可以承受高温和更大压力,适用于低粘度Hexply材料,即用于铺叠与机身壁板的同样M21-E增韧环氧预浸料。每台M Torres机床可以同时在殷钢芯轴上铺2个长为15m的梁,然后转移到热压罐中进行固化。
固化梁要使用自动台架TORRESONIC UT检测仪进行质量检查,该检测仪的检测范围长为15m,宽为2 m。MTorres公司制造框架和装上通用机器人,机器人由德国Kuka Roboter GMBH (Ausburg 德国)公司提供,电子设备由Techaton (Madrid 西班牙)供应。完成的梁部件运到Spirit公司位于苏格兰的Prestwick工厂,3段连接到一起,并与固定前缘和其他定位装置对接,然后交付完整的前缘组件给空客的Broughton工厂进行机翼总装。
2 后翼梁制造
后翼梁在GKN(Reddich Worchester英国)生产,MTorres公司提供了类似设备。由于该梁要和固定后缘对接,并要承当来自动翼的力,该公司除了制造梁以外,还负责将GE公司制造的固定机翼后缘(FTE)固定到后梁上。并进行最后检验,合格后重新将固定后缘分解,以便运输。
后梁包括3段,每段长为10m,最重要的是内侧的那段梁,重约500kg,其根部层压达25~30mm厚,中段梁重为150kg,最外的一段重为100kg。
每段梁都用纤维铺放机铺设,用殷纳钢模具。桶形的,固化后切成2个C形梁。材料是Hexcel的碳纤维环氧预浸料M-21E。带宽为0.64cm。前面已经提到所用铺放机也是M.Torres提供的,五坐标自动控制,模具固定在转动心轴上铺设。机器可按要求自动控制铺放厚度。铺设完后的热压罐固化和检验同前梁一样。
3 机翼上板件制造
机翼上部蒙皮在空客德国汉堡总部所属的空客Stade工厂生产,此处工房面积为30000m2,不但可铺碳纤维带,还第一次开发了玻璃纤维的铺设,该机翼板件31.6m×5.6m,所用热压罐是当前世界上技术最先进直径最大者之一,能同时固化2个板件。该热压罐据说直径是8m,而空客在制造A380时所用热压罐直径为6m。
除铺制机翼板件蒙皮外,该厂还生产用于该板件的长桁,为此该厂建了一条140m的生产线。在质量控制方面,引进了适用于该板件CFRP内外表面同时检查的的检查系统。对边缘的修整用水切割。在工房里建立了自动运输系统。
该全套设施也用于A350垂尾的制造。
4 机翼下板件制造
机翼下板件在西班牙Illescas 生产,所用技术条件、标准、工艺流程、设备与上板件一致。
上下机翼板件完工后均运至Broughton(英国)进行机翼装配。 Illescas还同时生产A350机身19段。
5 机翼固定后缘制造
机翼固定后缘由GE公司生产。后缘是蜂窝结构,原用Hexply8552预浸料胶接蒙皮和Hexcel蜂窝芯子Hexweb HRH-36,该芯子由Hexcel下料机加后交到GE公司。现在UMECO公司根据GE的要求开发了OOA的MTM-44-1预浸料,该新材料的特点是密度低,预制品密封袋装好后,抽真空并加温,130℃时开始固化,180℃时固化完成。挥发气少、孔隙率低。由于不需加压,可以不进热压罐,节约造价。
6 机翼前缘制造
机翼前缘在英国苏格兰 Spirit Aerosystems Europe的普雷斯蒂克工厂设计制造,部份零组件安排在其在马来西亚Subang工厂生产(如下板件)。该前缘长接近32m,其中50%是碳纤维构件。
7 中央翼制造
中央翼由EADS在Nante(法国南特)的工厂生产,40%的碳纤维(CFRP)件。翼盒长为6.5m,高为3.9m,表面面积为36m2,其板件是Nante生产过的最大复合材料件。技术标准、工艺流程、工艺方法基本和机翼部分一致。中央翼完工后运至法国St Nazaire,在那里和机身对接。
8 襟副翼制造
襟副翼也主要是复合材料结构。GKN公司承担为A350制造襟翼,该合同在德国幕尼黑签订。GKN又将承包的外襟翼转包给荷兰Stork Fokker公司生产,Fokker公司在Papendrecht制造外襟翼。内襟翼即由GKN在Bremen生产。
尾翼制造
空客德国Stade分部承担了A350尾翼的设计工作,并承担垂直尾翼的制造。尾翼整个是以碳纤维(CFRP)为主。Stade拥有强大的复合材料构件制造能力,除承当A350机翼上板件生产外还有足够的实力(包括设备)来完成垂尾制造计划。 西班牙的 Puero Real于2011年开始制造A350的水平尾翼,该处拥有强大的自动钻孔设备和铺放能力以及无损检测能力。
尾翼的方向舵,升降舵即通过西班牙安排在哈尔滨哈飞与空客合资的企业生产。该合资公司配备了铺带机及有关的检验设备。
结束语
A350的制造分工比较杂,其第一供应商参与总体设计并承包分工部件的整个部件设计,除自己承当部分制造任务外还将部分制造工作外扩到第二承包商,甚至还有第三承包商,但第二承包商以下都不再有设计权限。
总的情况是前机身在德国总成,中机身在美国总成,后机身也在德国总成,机翼在英国总成,尾翼在西班牙总成,中央翼在法国总成,这些总成单位就是当然的第一承包单位。最后都交到法国图鲁兹进行总装配。
总之,复合材料在飞机上的应用正日益增大,A350中52%的占有量虽是空前,但决非绝后。A350在铺带铺丝工艺上比A380又有许多突破。从当前复合材料构件制造来看,全工艺过程必须紧紧抓住铺放(铺带或铺丝)、机加铣切、钻孔、无损超声几个主要环节,缝合技术在机身后压力框等部件中已开始采用。随着A350-1000型的开发还正在研究一些更新的技术使用。
值得一提的是,空客还在考虑继续扩大复合材料使用范围,例如将发展的1000型,总长将比900型长7m,要增加 11个隔框。要减少由于增加隔框而相应增加过多重量,他们准备用BRaF (Braided Frame)即隔框编织法来制造这些复合材料隔框。其过程就是将干纤维带通过编织预成型件和机身直径相同的预成型件,然后注树脂,固化后修正成为框的成品,而不再通过预浸带来铺设。此外还在研究用FPP(Fiber Patch Perform),是一种干脆用纤维丝束小片的预成型法,它通过机械手来安放微小的补片,注入树脂制造零件,并用于零件(如窗口边缘)的局部加强,下一步计划是准备用于制造复合材料长桁的预成型件,使重量更轻、成本更低。而有关这些新技术所需新设备的充实和现代化又是个重要问题。
参考文献:
[1] 范玉青,张丽华.超大型复合材料机体部件应用技术的新进展.航空学报,2009,30(3):534-543.
[2] George M. Automating aerospace composites production with fiber placement. Reinforced Plastic,2011,55(3):31-37.
[3] Leeuwen M V.First A350XWB aft fuselage built[EB/OL]. 2012[2013-5-12].http://www.aviationnews.eu/2012/03/14/ first-a350-xwb-aft-fuselage-built/
[4] Gardiner G.A350 XWB Update: Smart manufacturing[EB/OL].2011[2013-5-16].http://www.compositesworld.com/articles/a350-xwb-update-smart-manufacturing.